هنگامی که اولین ویرایش کنترل خوردگی خط لوله توسط A.W. Peabody در سال 1967 منتشر شد، مقررات دولتی کمی برای مبارزه با آن وجود داشت. امروزه وزارت حمل و نقل-دفتر ایمنی خط لوله (DOT/OPS)، اداره ایمنی و بهداشت شغلی (OSHA) و وزارت منابع محیطی (DER) از جمله بسیاری از آژانس های نظارتی هستند که صنعت خط لوله را تحت تاثیر قرار داده یا کنترل می کنند.
مقررات دولتی، همراه با توسعه، معرفی و پذیرش پوششهای جدید خطوط لوله، تغییرات عمدهای ایجاد کرده است و همچنان بر انتخاب و استفاده از پوششهای خطوط لوله در آینده تأثیر خواهد گذاشت.
اقتصاد، در حالی که هنوز یک عامل است، با نگرانی های ایمنی و زیست محیطی جایگزین می شود تا بهترین سیستم های پوشش لوله موجود را به دست آورد. این روند برای اولین بار در اروپا آشکار شد، جایی که ماندگاری، به جای هزینه، منجر به استفاده از سیستم های چند لایه ای شد که ثابت کرده اند در طول عمر خط لوله موثرتر و مقرون به صرفه تر هستند. در محیط کنترل شده امروزی، تمام خطوط لوله خطرناک جدید (حمل نفت، گاز یا سایر مواد بالقوه خطرناک) طبق مقررات فدرال ملزم به استفاده از پوشش موثر و حفاظت کاتدی (CP) هستند.
اثربخشی پوشش ها به عنوان وسیله ای برای کنترل خوردگی
اولین تلاش ها برای کنترل خوردگی خط لوله بر استفاده از مواد پوششی و این استدلال بود که اگر فلز خط لوله بتواند از تماس با زمین اطراف ممانعت شود، هیچ خوردگی رخ نمی دهد. این مفهوم کاملاً معقول و منطقی است. علاوه بر این، یک پوشش به عنوان وسیله ای برای جلوگیری از خوردگی کاملاً مؤثر خواهد بود اگر مواد پوشش:
- یک عایق الکتریکی موثر باشد،
- بدون هیچ گونه پارگی قابل اعمال باشد و در طی فرآیند پر کردن و پس از پر کردن به همین صورت باقی بماند.
- یک فیلم در ابتدا کامل است که با گذشت زمان به همین شکل باقی خواهد ماند.
در حالی که این امر با برخی از سیستم های چند لایه پیشرفته امکان پذیر باشد، ممکن است از تحلیل هزینه اولیه عملی نباشد.
اگرچه پوشش ها به خودی خود ممکن است یک پاسخ کامل برای کنترل خوردگی نباشند، اما زمانی که به درستی استفاده شوند بسیار موثر هستند. اکثر اپراتورها پوشش و حفاظت کاتدی (CP) را برای تمام خطوط لوله خود به طور طبیعی برنامه ریزی می کنند. یک پوشش مناسب انتخاب شده و اعمال شده، تمام محافظت لازم را در بیشتر سطح خط لوله که روی آن اعمال می شود، فراهم می کند. در یک خط لوله معمولی با پوشش خوب، این باید بهتر از 99٪ باشد و همراه با CP، باید حفاظت کامل را ایجاد کند.
هدف این فصل ارائه توصیه های خاصی برای مواد پوششی نیست که باید استفاده شوند. با این حال، قابلیت ها و محدودیت های مواد مختلف پوشش خط لوله و همچنین ویژگی های مطلوب و چگونگی استفاده حداکثری از هر ماده مورد استفاده مورد بحث قرار خواهد گرفت. انواع پوششهایی که اکنون در سیستمهای خط لوله استفاده میشوند به اختصار توضیح داده میشوند.
استاندارد NACE RP0169-96 بخش 5: پوششها، راهنمای جامعی برای پوششهای لوله است و برای درک بهتر اهمیت آن ها باید مطالعه شود. این استاندارد ویژگی های مطلوب پوشش های زیر را فهرست می کند:
- عایق الکتریکی موثر. از آن جایی که خوردگی خاک یک فرآیند الکتروشیمیایی است، پوشش لوله باید با جداسازی لوله از محیط نصب شده/الکترولیت، حرکت جریان را متوقف کند. برای اطمینان از مقاومت الکتریکی بالا، پوشش باید استحکام دی الکتریک بالایی داشته باشد.
- مانع رطوبت موثر. برخلاف این نظریه که جذب آب خوب است زیرا کارایی CP را افزایش می دهد، انتقال آب از طریق پوشش ممکن است باعث ایجاد تاول شود و با جلوگیری از جدایش باعث خوردگی شود.
- کاربرد.اعمال پوشش روی لوله باید به روشی امکان پذیر باشد که بر خواص لوله تأثیر منفی نگذارد و دارای حداقل نقص و خرابی باشد.
- توانایی مقاومت در برابر گسترش منافذ با گذشت زمان.پس از دفن پوشش، دو ناحیه ای که ممکن است پوشش ها را تخریب کنند، تنش خاک و آلاینده های خاک هستند. تنش خاک که در خاک های خاصی که به طور متناوب مرطوب و خشک هستند ایجاد می شود، نیروهایی را ایجاد می کند که ممکن است پوشش را شکافته یا باعث ایجاد مناطق نازک شود. برای به حداقل رساندن این مشکل، باید مقاومت سایشی، استحکام کششی، چسبندگی و چسبندگی پوشش را ارزیابی کرد. مقاومت پوشش در برابر مواد شیمیایی، هیدروکربن ها و شرایط اسیدی یا قلیایی باید برای ارزیابی عملکرد آن ها در خاک های آلوده شناخته شود.
- چسبندگی خوب به سطح لوله. پوشش لوله به چسبندگی کافی برای جلوگیری از ورود آب یا مهاجرت بین پوشش و لوله، همراه با چسبندگی برای مقاومت در برابر دست زدن و تنش خاک نیاز دارد. تنش خاک عامل اصلی خرابی پوشش لوله است. اثرات تنش خاک را می توان بر روی پوشش های پلی اتیلن انعطاف پذیر با چسب الاستومری به صورت چین و چروک مشاهده کرد. با این حال، انواع دیگر پوششها میتوانند با تاول زدن اپوکسی با پیوند همجوشی (FBE) یا ترک خوردگی پوشش قطران زغال سنگ انامل (CTE) که با حرکت خاک تشدید میشوند، از بین بروند. مقاومت در برابر برش باید با اندازه گیری مقاومت ماده پشت بند (یا پوشش بیرونی) در برابر تغییر شکل و نیروی کششی ترکیب شود. این دو ویژگی برای تعیین توانایی پوشش خط لوله برای مقاومت در برابر آسیب به حرکت خاک ترکیب می شوند. مقاومت در برابر تنش خاک با مقاومت برشی اندازه گیری می شود نه با مقاومت پوسته شدن.
- توانایی مقاومت در برابر حمل، ذخیره سازی (تخریب UV) و نصب. توانایی یک پوشش برای مقاومت در برابر آسیب تابعی از خواص ضربه، سایش و انعطاف پذیری آن است. پوششهای لوله در معرض دستکاریهای متعددی بین کاربرد و پس از پر کردن هستند. توانایی این پوشش ها برای مقاومت در برابر این نیروها به طور قابل توجهی متفاوت است، بنابراین این عوامل باید ارزیابی شوند تا بدانیم آیا باید از اقدامات احتیاطی خاصی استفاده شود یا خیر. اشعه ماوراء بنفش می تواند برای پوشش لوله ها بسیار مخرب باشد. مدت زمان نگهداری ممکن است از 6 ماه تا 5 سال متغیر باشد، بنابراین مقاومت در برابر اشعه ماوراء بنفش یک نکته بسیار مهم است.
- توانایی حفظ مقاومت الکتریکی قابل ملاحظه ثابت با گذشت زمان.مقاومت الکتریکی موثر یک پوشش در هر فوت مربع متوسط به موارد زیر بستگی دارد.
- مقاومت مواد پوشش
- ضخامت پوشش
- مقاومت در برابر جذب رطوبت
- مقاومت در برابر انتقال بخار آب
- تعداد و اندازه منافذ
- مقاومت الکترولیت
- چسبندگی یا چسبندگی پوشش
- اگر مقاومت موثر ناپایدار باشد، CP مورد نیاز ممکن است هر چند سال یکبار دو برابر شود. اگر خاک در اطراف خط لوله ته نشین نشده باشد و اگر رطوبت تا هر حفره در پوشش نفوذ کرده باشد، اندازه گیری مقاومت بالاتر گمراه کننده راحت به دست می آید.
برای ارزیابی اعتبار این اندازهگیریهای مقاومت و استفاده از آن ها برای طراحی سیستم CP، تجربه لازم است.
8. مقاومت در برابر گسستگی.
از آن جایی که اکثر خطوط لوله به صورت کاتدی محافظت می شوند، پوشش باید با CP سازگار باشد. مقدار CP مورد نیاز مستقیماً با کیفیت و یکپارچگی پوشش متناسب است. جنبه های منفی CP این است که ممکن است آب را از طریق پوشش عبور دهد و نیروی پیوندی بین اطراف منافذ ممکن است تمایل به جدا شدن داشته باشد. هیچ پوششی در برابر آسیب CP کاملاً مقاوم نیست. هنگامی که مقدار زیادی جریان مورد نیاز است، جریان سرگردان و مشکلات تداخل ممکن است ایجاد شود. این امر بر اهمیت انتخاب پوشش، کاربرد و نصب مناسب تأکید می کند.
9. سهولت تعمیر.
از آن جایی که پوشش کامل لوله وجود ندارد، می توان انتظار داشت که برخی تعمیرات میدانی و همچنین پوشش میدانی ناحیه جوش انجام شود. سازگاری را بررسی کنید و توصیه های سازنده را دنبال کنید. تعمیر میدانی هرگز به خوبی پوشش اصلی نیست. بازرسی دقیق حین تعمیر بایستی حفظ شود.
10. تعامل غیر سمی با محیط زیست.
برخی از مواد پوشش به دلیل استانداردهای زیست محیطی و بهداشتی اصلاح، محدود یا ممنوع شده اند. پشم های آزبستی و پرایمر با حلالهای خاص نیاز به جایگزینی با تقویتکنندههای شیشهای و اصلاح حلالها دارند. تغییرات در پودرهای اپوکسی با پیوند همجوشی برای از بین بردن عوامل سرطان زا نیز به دلیل نگرانی های بهداشتی و زیست محیطی ضروری است. این تأثیر عمده ای از تغییر بر روی پوشش های لوله های امروزی بوده است.
علاوه بر ویژگی های فوق، فاکتورهای معمولی زیر هنگام انتخاب پوشش لوله باید در نظر گرفته شود.
- نوع محیط
- دسترسی به خط لوله
- دمای عملیاتی خط لوله
- دمای محیط در طول کاربرد، ذخیره سازی، حمل و نقل، ساخت و نصب و راه اندازی
- موقعیت جغرافیایی و فیزیکی
- نوع پوشش روی خط لوله موجود
- حمل و نقل و انبارش
- روش های نصب
- هزینه ها
- الزامات آماده سازی سطح لوله
عملکرد خوب در کار کنترل خوردگی خطوط لوله مدرن شامل استفاده از پوشش های خوب در ترکیب با CP به عنوان خطوط اصلی دفاعی است. روش های تکمیلی، مانند استفاده از کوپلینگ های عایق و کنترل محیطی محلی ممکن است برای تقویت این روش های کنترل اساسی استفاده شود.
در انتخاب یک سیستم پوشش برای یک پروژه خط لوله معین، یکی از مهمترین ویژگی هایی که باید برای آن طراحی شود، پایداری است. منظور از ترکیب پوششی است که پس از نصب خط لوله پر شدن لوله پایدار بماند و در طول زمان کمترین مقاومت الکتریکی را از دست بدهد.
این ویژگی ها در هر صورت مهم هستند، اما به ویژه در مواردی که CP برای تکمیل پوشش استفاده می شود. هنگامی که از یک پوشش ناپایدار استفاده می شود، یک سیستم CP که در طول عمر اولیه یک خط لوله کاملاً کافی است، ممکن است دیگر محافظت کامل را به دلیل خرابی پوشش (همان طور که با کاهش مقاومت الکتریکی موثر پوشش نشان می دهد) ارائه نکند که فرایند cp به جریان اضافه احتیاج دارد. این بدان معناست که هزینههای مستمر برای نصب CP اضافی ضروری خواهد بود. اقتصاد کلی مفهوم پوشش مضاعف CP تحت تأثیر عملکرد ضعیف پوشش قرار می گیرد.
در بررسی 50 سال مقالات در مورد پوشش خطوط لوله، مفاهیم زیر پدیدار شد:
- انتخاب بهترین پوشش و کاربرد مناسب بسیار مهم است.
- CP برای محافظت 100% باید فرایند پوشش دهی را کامل کند.
- تست های زیر زمینی از تست های آزمایشگاهی قابل اعتمادتر هستند.
- نتایج آزمایشات چسبندگی با نتایج آزمایشهای جدایش کاتدی ارتباطی ندارد.
- تست های جدایش کاتدی بهترین آزمایش برای اندازه گیری عملکرد پوشش هستند.
- جریان مورد نیاز برای CP بهترین معیار برای عملکرد پوشش است.
- ضخامت بهینه پوشش اهمیت دارد.
- تنش خاک یکی از مشکلات اصلی است.
- مقاومت در برابر جدایش کاتدی و تنش خاک از الزامات بسیار مهم هستند
- از یک پوشش لوله برای اینکه پوشش لوله موثر باشد، باید این الزمات را رعایت کند: چسبندگی، ضخامت کافی، جذب/انتقال کم رطوبت، مقاومت شیمیایی (به ویژه مواد قلیایی حاصل از CP)، و انعطاف پذیری.
- انتخاب بهترین سیستم مناسب مهم است، اما کاربری مناسب مهم ترین نکته است.
یکی از دلایل اصلی پارگی پوشش خط لوله، استفاده نادرست است. یک ماده با کیفیت که بد به کار رفته است ارزش کمی دارد و کیفیت پوشش لوله فقط به اندازه کیفیت کاربرد است. برای کمک به ارزیابی یک کاربر، نکات زیر باید در نظر گرفته شود.
1. تجربه.
تحقیق و آزمون و خطا در توسعه هر پوشش با همکاری نزدیک بین اپراتور، سازنده پوشش، سازنده تجهیزات و مشتری انجام شود. انتقال از آزمایشگاه به خط تولید معمولاً یک تجربه پرهزینه است که نباید نادیده گرفته شود.
2. شهرت.
این یک دارایی است که با عملکرد ثابت به دست می آید. نه تنها کار با کیفیت خوب، بلکه حل مشکلات و تصحیح اشتباهات به ایجاد شهرت کمک می کند.
3. قابلیت اطمینان.
متغیرهای زیادی بر کاربرد پوشش ها تأثیر می گذارد. نیروی کار قابل اعتماد، تجهیزات به خوبی نگهداری شده و عملکرد با کیفیت ثابت پیش نیازهای یک اپلیکاتور هستند. حداقل مشخصات تعیین شده سازنده برای کاربرد مواد باید رعایت شود.
4. تجهیزات مدرن خودکار.
هزینه برای تجهیزات کاربردی خودکار بخش مهمی از موفقیت پوشش های پلاستیکی است. حذف خطاهای انسانی از طریق اتوماسیون و کنترل همچنان عامل مهمی در بهبود پوشش لوله است.
5. کنترل کیفیت.
مطابقت با مشخصات باید به طور منظم بررسی شود. آگاهی از رویه های کنترل کیفیت اپلیکاتور در مورد مواد، کاربرد و محصول نهایی در انتخاب اجرا کننده ضروری است.
مشخصات فنی
پوشش خط لوله نباید بدون مشخصات سفت و سخت انجام شود که دقیقاً هر مرحله از روش پوشش مورد استفاده را مشخص می کند. چنین مشخصاتی لازم است تا اطمینان حاصل شود که مواد مورد استفاده به گونه ای اعمال می شوند که امکان توسعه بهترین پوششی که آن مواد قادر به انجام آن هستند را فراهم کند.
از آن جایی که ممکن است از مواد زیادی استفاده شود، در این جا نمونه خاصی از مشخصات پوشش مورد استفاده قرار نخواهد گرفت. مشخصات را می توان مطابق با توصیه های سازنده با تغییراتی که ممکن است توسط شرایط مربوط به پروژه خاص و الزامات سیستم خط لوله ای که لوله پوشش داده شده در آن استفاده می شود ، تهیه کرد.
مناطق تحت پوشش باید مشخصات زیر را داشته باشند:
- تمیز کردن سطح لوله
- بتونه کاری، در صورت نیاز
- مواد پوشش مورد استفاده و (اگر بیش از یک ماده) ترتیب استفاده از آن ها
- ضخامت کل با تلورانس های مجاز
- مشخصات مربوط به مواد خاصی که باید استفاده شود، مانند دما و ضخامت کاربرد، کشش (برای نوارها یا لفافها) و سایر موارد با ماهیت مشابه
- الزامات رسیدگی به مواد پوشش دهنده، مانند شرایط نگهداری و شرایط خشک و تمیز
- الزامات بازرسی
- رویه تعمیر عیوب پوشش
- اساس رد پوشش غیرقابل قبول
- الزامات برای جابجایی و حمل و نقل لوله پوشش داده شده
- جزئیات پوشش سرجوش میدانی زمانی که از لوله های پوشش داده شده کارخانه ای استفاده می شود
- الزامات پر کردن لوله
مراحل بازرسی
هنگامی که سیستم پوشش و اجرا کننده انتخاب شد، بخش مهمی از نصب با کیفیت، بازرسی خوب در پروژه است. بازرسی باید با انباشت لوله لخت از طریق عملیات پوشش دهی، بارگیری، ذخیره لوله پوشش داده شده، بازرسی میدانی، روش پوشش سرجوش و پر کردن لوله پوشش داده شده آغاز شود. دانش سیستم پوشش، امکانات کارخانه، روش های کنترل کیفیت، الزامات حمل و نقل، جابجایی، پوشش سرجوش، شرایط میدانی، تشخیص منافذ در پروژه و تعمیر، الزامات مورد نیاز برای نصب صحیح هستند. تجربه و عقل سلیم در تفسیر مشخصات و تجزیه و تحلیل نتایج آزمایش به دستیابی به بهترین نتایج پوشش ممکن کمک می کند.
به عنوان یک نسخه پشتیبان نهایی برای نظارت بر برنامه که توسط بازرس پوشش اعمال می شود، عملیات معمول خط لوله شامل آزمایش نهایی با یک آشکارساز هالیدی است. این دستگاه یک ولتاژ الکتریکی را در سراسر پوشش اعمال می کند. یک الکترود روی کل سطح پوشش عبور داده می شود و با عبور از روی یک نقص پوشش، تخلیه الکتریکی بین الکترود و لوله ایجاد می شود. این تخلیه یا جرقه، توسط یک دستگاه سیگنال میفرستد که به اپراتور هشدار می دهد که منفذ تشخیص داده شده است. اپراتور نقص را برای تیم تعمیر مشخص می کند و ادامه می دهد.
هنگام بررسی منافذ، به مشخصات مناسب NACE مراجعه کنید: RP02-74) آخرین ویرایش) برای پوشش های ضخیم تر، یا RP04-95) آخرین ویرایش) برای سیستم های پوشش نازک تر.
بازرسی منافذ در پوشش کارخانه
لوله های پوشش داده شده در یک کارخانه پوشش معمولاً قبل از ارسال از یک آشکارساز هالیدی عبور می کنند. هم لولههای با پوشش کارخانه ای و هم لولهای که روی گودال پوشش دهی شدهاند، باید قبل از قرار گرفتن در گودال، تحت آزمایش نهایی هالیدی قرار گیرند.
هر چه عیوب در پوششی که قرار است تعمیر شود کمتر باشد، پوشش تکمیل شده کیفیت بهتری دارد. با این وجود، اگر همه منافذ توسط یک آشکارساز در شرایط عملیاتی مناسب انتخاب شوند، و اگر آن ها برای انطباق با یک روش موثر تعمیر شوند، آنگاه کیفیت پوشش هنگام ورود به گودال حداقل به حد مطلوب نزدیک می شود.
بازرسی میدانی هالیدی
چندین نوع آشکارساز هالیدی برای استفاده میدانی در محل ساخت خط لوله مناسب هستند. رایج ترین آن ها معمولاً با باتری کار می کنند و مجهز به نوعی الکترود دور لوله هستند. الکترود طوری چیده شده است که ممکن است حلقه توسط اپراتور در امتداد لوله رانده یا بغلتد و به الکترود اجازه دهد تا تمام قسمت های سطح پوشش را اسکن کند.
آشکارساز هالیدی باید مطابق با دستورالعمل های سازنده کار کند. بازرس پوشش باید مطمئن شود که اپراتور به درستی آموزش دیده است و از تجهیزات به درستی استفاده می کند. برخی از روش های عملیاتی که برای هر نوع مکان یاب هالیدی اعمال می شود شامل موارد زیر است.
- در مدل هایی که با باتری کار می کنند، فقط از باتری هایی با شارژ کافی استفاده کنید.
- از آشکارسازهایی استفاده کنید که با ولتاژ مناسب برای پوشش اعمال شده تنظیم شده اند. پوششهای ضخیم به ولتاژ بالایی نیاز دارند تا در هنگام سوراخ جرقه بزنند. از طرف دیگر، ولتاژ بسیار بالا ممکن است پوشش های فیلم نازک مانند نوارها یا سایر پوشش های پلاستیکی نازک را از بین ببرد.
- به طور دوره ای بررسی کنید که آشکارساز به درستی کار می کند. این ممکن است با ایجاد عمدی سوراخ در پوشش (مانند سوراخ سوزنی که با چاقو ساخته شده است) و عبور آشکارساز از روی سوراخ انجام شود. عدم تشخیص درست سوراخ نشان دهنده نیاز به تنظیم اصلاحی سریع است. در طول کار تولید، کنترل باید حداقل دو بار در روز و در مواقع دیگری انجام شود که بازرس ممکن است به عملکرد ضعیف مشکوک شود.
- الکترودهای تماسی را تمیز نگه دارید. تجمع مواد پوشش روی الکترودها ممکن است در تشخیص کارآمد اختلال ایجاد کند یا حتی از آن کاملاً جلوگیری کند. این امکان در مورد برخی مواد بیشتر از سایرین است. در مواردی که فاکتوری وجود دارد، باید بر تمیز نگه داشتن الکترودها از مواد پوشش عایق تاکید شود.
- یک زمین خوب را حفظ کنید. برای کامل شدن، مدار آشکارساز باید با زمین، مثلاً با یک سیم زمین ، تماس داشته باشد. این سیم باید هر روز از نظر آسیب بررسی شود و در صورت معیوب بودن تعویض یا تعمیر شود. هنگام کار بر روی بخش های طولانی خط، معمولاً رسانایی کافی بین خط و زمین وجود دارد تا امکان عملکرد کافی آشکارساز را فراهم کند. از سوی دیگر، ممکن است برای ایجاد یک مدار کافی، طول کوتاهی از لوله با پوشش خوب روی لغزشهای خشک به لوله متصل شود.
انواع پوشش های خط لوله
انواع پوشش های خط لوله و ویزگی های آن ها در جدول زیر خلاصه شده است.
پوشش لوله | ویژگی های مطلوب | محدودیت ها |
---|---|---|
قطران زغال سنگ | 80 سال استفاده حداقل حساسیت نسبت به منافذ جریان پایین مورد نیاز مقاومت خوب در برابر جدایش کاتدی چسبندگی خوب به استیل | محدودیت های سازنده محدودیت های اپراتور نگرانیهای کیفیت هوا و سلامتی تغییر در تقویت کننده های مجاز |
سیستم های نوارهای اعمال شده کارخانه ای | 30 سال استفاده حداقل حساسیت نسبت به منافذ سهولت استفاده چسبندگی خوب به استیل انرژی کم مورد نیاز برای استفاده | محدودیت های رسیدگی - حمل و نقل و نصب تاول زدن حرارتی و UV –پتانسیل ذخیره محافظت CP از خاک استحکام پارگی |
پیوند اکسترود شده پلی الفین با چسب آسفالت/بوتیل | 40 سال استفاده حداقل حساسیت نسبت به منافذ جریان کم مورد نیاز سهولت استفاده بدون آلودگی انرژی کم مورد نیاز برای استفاده | حداقل چسبندگی به استیل ذخیره سازی محدود (به جز کربن اکتیو) تمایل به انتشار پارگی در طول لوله |
دو طرف اکسترود شده پلی الفین با چسب بوتیل | 25 سال استفاده کم ترین حساسیت به منافذ جریان کم مورد نیاز چسبندگی خوب به استیل سهولت کاربرد بدون آلودگی انرزی کم مورد نیاز برای استفاده | حذف شدن سخت پوشش کاربرد محدود |
پیوند هم جوشی | 35 سال استفاده جریان کم مورد نیاز مقاومت عالی در بر ابر جدایش کاتدی چسبندگی عالی به استیل مقاومت عالی به هیدروکربن ها | پارامترهای کاربردی دقیق دمای کاربردی بالا با توجه به عیوب سطح لوله فولادی مقاومت در برابر ضربه و سایش کمتر جذب رطوبت بالا |
اپوکسی چند لایه/سیستم پلی الفین اکسترود شده | نیاز به جریان پایین مقاومت بالا به جدایش کاتدی چسبندگی عالی به استیل مقاومت عالی به هیدروکربن ها مقاومت بالا نسبت به ضربه و سایش | کاربرد محدود پارامترهای کاربردی دقیق هزینه اولیه بالاتر محافظ احتمالی جریان CP |
انامل ها
انامل های قیری امروزه از قطران زغال سنگ با میزان کم کربن فرموله می شوند که با تجزیه زغال سنگ و تقطیرهای مواد آروماتیک سنگین قطران زغال سنگ و به دنبال آن یک پرکننده معدنی بی اثر، می باشد. آسفالت های نفتی با آسفالت های منتخب با هوا هنوز در سطح بین المللی به عنوان پوشش لوله استفاده می شود، اما امروزه استفاده از آنها در آمریکای شمالی تقریباً وجود ندارد.
پوششهای اولیه انامل قطران زغالسنگ (CTE) معمولاً دارای یک پوشش بیرونی از نمد پارچهای بودند تا یک محافظ پر کننده ایجاد کنند. با این حال، نمد پارچه ای مانع از تمایل CTE به خزش و جریان سرد تحت تنش خاک در محدوده دمای عملیاتی بالاتر خط لوله نمیشود. استفاده از نمد آزبست این مشکل را به حداقل رساند، اما ساخت پوشش های آزبستی متوقف شده است. در حال حاضر از پوشش های فیبر شیشه ای پیوند شده به رزین استفاده می شود. سیستمهای CTE بیش از 80 سال است که مورد استفاده قرار گرفتهاند، و یک پرایمر اپوکسی دو جزئی که اخیراً معرفی شده است، هنگام استفاده با مینای ویژه با کاربری گرم، دمای در معرض یک سیستم پوشش CTE را به 230 ± درجه فارنهایت افزایش داده است. امروزه یک تشک فیبر شیشه ای داخلی و خارجی به طور همزمان با استفاده از CTE داغ در سیستم پوشش CTE گنجانده شده است. تشک شیشه ای داخلی به مرکز پوشش کشیده می شود. روکش فیبر شیشه ای بیرونی و درونی معمولاً با قطران زغال سنگ از قبل اشباع می شود تا به خیس شدن کمک کند و به سطح بیرونی CTE کشیده می شود. پوششهای تقویتکننده بیرونی بسیار سنگین با رشتههای شیشهای بافته شده و پوشش های شیشهای متصل به رزین برای محافظت بیشتر در برابر اثرات تنش خاک ایجاد شدهاند.
ماستیک آسفالت اکسترود شده
بیش از 75 سال پیش معرفی شد، این مخلوط غلیظ (2/1 تا 8/5 اینچ [1.2 تا 1.6 سانتیمتر])، مخلوط متراکم از شن و ماسه درجه بندی شده، سنگ آهک خرد شده و الیاف شیشه که با آسفالت دمیده شده با هوا چسبانده شده است تا یک پوشش لوله با کیفیت بالا ارائه دهد. با این حال، وزن، هزینه و در دسترس بودن محدود آن باعث شد که تولید آن متوقف شود.
سیستم های پوشش نواری کارخانه ای
برای اولین بار بیش از 65 سال پیش از نوارهای با روکش پترولاتوم تقویت شده با پارچه استفاده شد. نوارهای پلی اتیلن برای پوشش خطوط لوله 46 سال پیش و سیستم های نواری کاربردی کارخانه ای 20 سال پیش معرفی شدند. سیستمهای نواری کارخانه ای از یک پرایمر، یک لایه نوار داخلی جلوگیری از خوردگی و یک یا دو لایه بیرونی برای محافظت مکانیکی تشکیل شدهاند. نگرانی در مورد محافظ CP بر روی یک پوشش از هم گسیخته منجر به توسعه سیستم های نواری چند لایه ذوب شده و همچنین پشتیانی شده است که CP را محافظت نمی کند. محدودیت های زیست محیطی پرایمرهای مبتنی بر حلال با معرفی پرایمرهای قابل قبول از نظر زیست محیطی در حال رفع است. علیرغم این محدودیتها، در دسترس بودن، سهولت کاربرد و هزینه به این معنی است که استفاده از سیستمهای نواری کاربردی ادامه خواهد یافت.
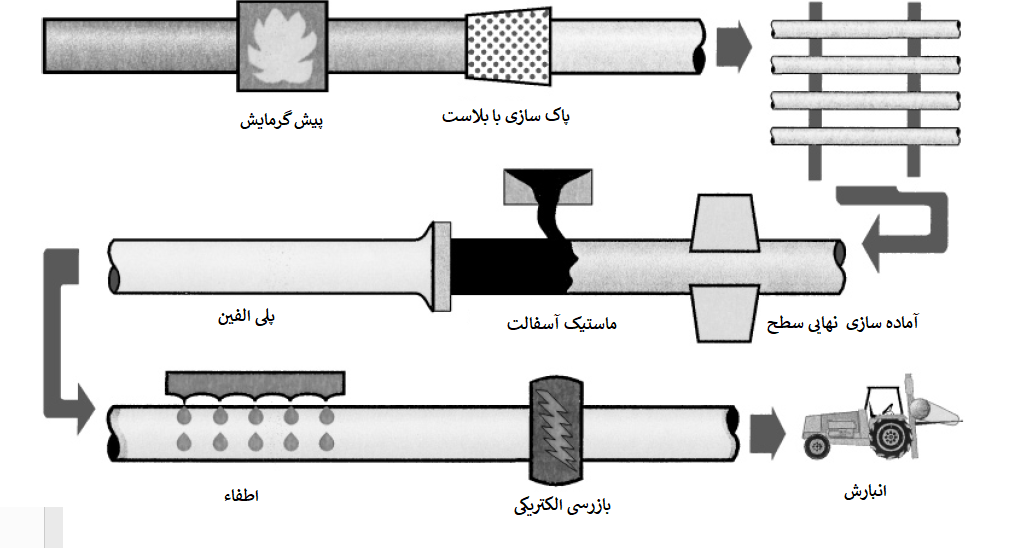
شماتیک کاربرد پلی الفین اکسترود شده با ماستیک آسفالت
سیستم های پلی الفین اکسترود شده
اولین سیستم پلی الفین اکسترود شده در سال 1956 به عنوان پلی اتیلن اکسترود شده مشبک روی چسب ماستیک آسفالت معرفی شد. این ماده که در ابتدا برای لوله های با قطر کوچک تا 11.4 سانتی متر معرفی شد، اکنون برای لوله های تا 61 سانتی متر در دسترس است.
قطر؛ محبوب ترین اندازه 16 اینچ (40.6 سانتی متر) است. بهبودهای اخیر در چسب باعث چسبندگی بهتر می شود و انتخاب پلی اتیلن مقاومت به ترک تنشی را افزایش داده است.
این سیستم ها که با پلی پروپیلن برای استفاده در دماهای بالاتر (تا 190 ± فارنهایت [88 ± درجه سانتی گراد]) در دسترس هستند، از اواسط دهه 1960 همراه با روش اکستروژن جانبی برای قطرهای بزرگتر تا 60 اینچ (152.4 سانتی متر) در اروپا استفاده شده است . یک چسب کوپلیمر برای از بین بردن جریان سرد و به حداقل رساندن جمع شدن پوشش استفاده می شود. به دنبال آن از پرایمر اپوکسی استفاده می شود. در اواخر سال 1972 روش اکستروژن جانبی در ایالات متحده معرفی شد. این یک اکستروژن دو طرفه است که در آن چسب لاستیک بوتیل بر روی لوله اکسترود می شود و به دنبال آن اکسترود پلی اتیلن انجام می شود. اکستروژن جانبی میتواند لولههایی به قطر 145 اینچ (368 سانتیمتر) را بپوشاند که تنها محدودیت آن تمیز کردن و ظرفیت جابجایی لوله است. فرآیند اکستروژن یک روش تولید قابل اعتماد با کنترل های دقیق است. اکسترودر مواد را در دما و فشار دلخواه گرم می کند، ذوب می کند، مخلوط می کند و بر روی لوله فولادی اکسترود می کند.
سیستم های اکستروژن غیر سمی هستند و کیفیت هوا را کاهش نمی دهند. استفاده از این سیستم ها به دلیل قابلیت کنترل پذیری، مقاومت در برابر رطوبت و قابلیت تکرارپذیری کلی به رشد خود ادامه خواهد داد.
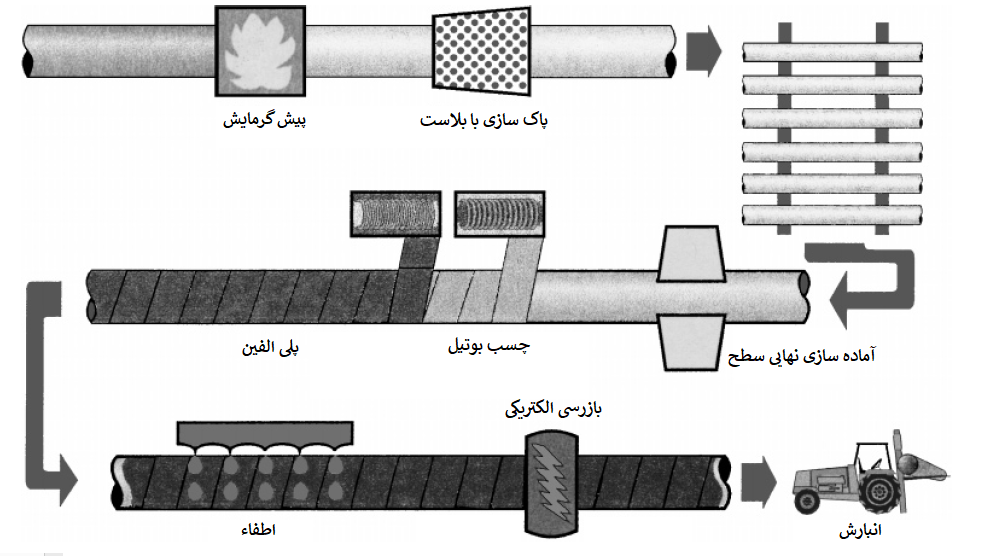
شماتیک کاربردی طرف پلی الفین اکسترود شده رو به طرف چسب بوتیل اکسترود شده
اپوکسی با پیوند هم جوشی
پوششهای اپوکسی با پیوند هم جوشی (FBE) برای اولین بار در اواخر سال 1961 به صورت تجاری در دسترس بودند. برای سالهای متمادی این پوششها تنها در لولههای با قطر 1.9 تا 21.9 سانتیمتر در دسترس بودند، اما اکنون برای لولهکشی در آمریکای شمالی با قطر بالای 48 اینچ (122 سانتی متر) در دسترس هستند. برای سال های متمادی FBE در 8-10 مایل (203.2-254.0 µm) اعمال می شد تا با سایر پوشش ها رقابت کند. در حال حاضر، آن را در حداقل 12 مایل تا 25 مایلی (304.8-635 µm) اعمال می شود. در طی 35 سال گذشته، رزین ها از طریق نیاز پرایمر و برخی کاربردهای حرارتی، تکامل یافته اند. هیچ یک از پوشش های اپوکسی لوله فعلی نیازی به پرایمر ندارند و اکثر کاربردهای کارخانه ای به حرارت پس از استفاده نیاز ندارند. اکثر پودرهای پوشش لوله FBE در 18 سال گذشته ثابت مانده اند. سیستم های FBE دوگانه جدیدتر در اوایل دهه 1990 برای بهبود مقاومت در برابر جذب رطوبت و سایش معرفی شدند.
پوشش های FBE به دقت زیادی نیاز دارند تا به درستی اعمال شوند. علاوه بر روکش فلزی تقریباً سفید NACE شماره 2، شستشوی فسفات و شستشو با آب غیر معدنی برای حذف آلودگی احتمالی کلرید و بهبود خواص عملکرد ضروری است. از جمله مزایای FBE این است که هیچ عیب فولادی موجود را نمی پوشاند، بنابراین اجازه بازرسی لوله را پس از اعمال FBE می دهد. مقاومت در برابر تنش خاک و جداشدگی کاتدی FBE را به مشخص ترین پوشش لوله در ایالات متحده تبدیل کرده است. روند به سمت برنامه های کاربردی ضخیم تر است که 16 مایل (406.4 µm) معمول است. FBE در آینده نزدیک به اهمیت خود ادامه خواهد داد اما به تدریج این موقعیت را با سیستم های پوشش پلی اولفین اکسترود شده بهبودیافته و سیستم های پوشش چند لایه (FBE-extruded polyolefin) تقسیم خواهد کرد.
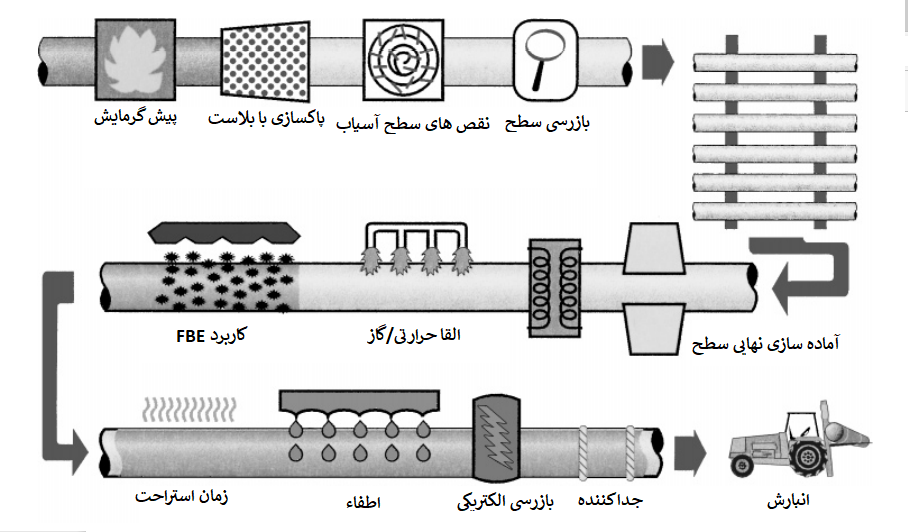
شماتیک کاربردی پودر اپوکسی با پیوند هم جوشی
سیستم های پوشش مایع
قطران زغال سنگ اپوکسی و اورتان ها در حال حاضر پرمصرف ترین سیستم های پوشش دهی لوله مایع هستند. آن ها در پوشش های سفارشی یا سیستم های کارخانه ای اصلاح شده، معمولاً روی لوله های با قطر بزرگتر یا لوله های چدن شکل پذیر که ممکن است با کارخانه های پوشش لوله موجود سازگار نباشند، اعمال می شوند.
مشخصات سازنده های خاص باید با تاکید بر تمیز کردن سطح، آماده سازی و زمان های استراحت و پوشش کاملاً رعایت شود.
این سیستم ها دائما در حال تکامل هستند. بیشترین رشد در استفاده از سیستم های اورتان بوده است.
سیستم های چند لایه اپوکسی/ پلی الفین اکسترود شده
اولین بار در اواسط دهه 1960 در اروپا به عنوان یک چسب سخت تحت پلی اتیلن معرفی شد و به دنبال آن یک پرایمر اپوکسی (FBE یا مایع) اضافه شد، سیستم های چند لایه اپوکسی/پلی الفین پر استفاده ترین سیستم های پوشش لوله در اروپا هستند. این سیستم ها در حال حاضر در سراسر جهان در دسترس هستند.
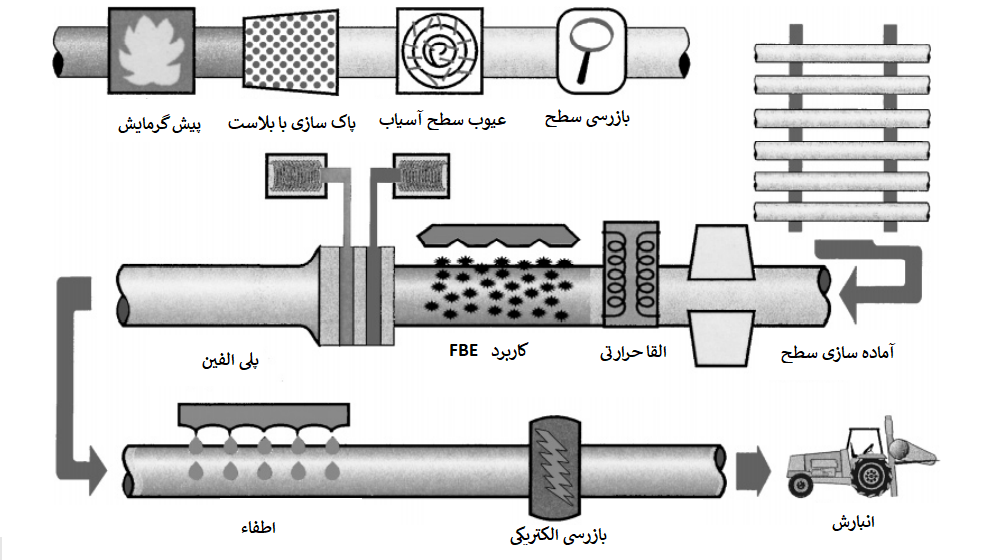
شکل شماتیک کاربرد پوشش کو پلیمر 3 لایه
نتیجه گیری
در خلاصه کردن این مطالب در مورد پوشش ها، مهندسان خوردگی خط لوله باید بر دو حوزه دانش تأکید کنند:
* اطلاعات کامل در مورد تمام جزئیات ویژگی ها، عملکرد و محدودیت های پوشش های در نظر گرفته شده برای پروژه های مختلف خط لوله.
* خلاصه ای کامل از شرایط موجود در طول مسیر پروژه های خط لوله پیشنهادی همراه با اطلاعاتی در مورد نحوه بهره برداری از خط لوله.
هنگامی که مهندسان خوردگی در این موارد به خوبی مطلع شوند، می توانند به طور موثر در انتخاب سیستم های پوشش محافظ مناسب مدیریت داشته باشند. آنها همچنین قادر خواهند بود مشخصات کاربردی را آماده کنند و برنامه های بازرسی را برنامه ریزی کنند که در صورت اجرای موثر، بهترین پوشش ممکن را تضمین می کنند.