در 50 سال گذشته شبکه های بزرگ خطوط لوله نفت و گاز با سیستم های پوشش دهی متنوع نصب شده اند. سیستمهای محافظ در برابر خوردگی - مانند نوارها، روکش های حرارتی جمعشونده و پوششهای مایع (پلیاورتان و اپوکسی) در همه نوع و اندازه خطوط لوله مدفون استفاده شده است. کیفیت یک سیستم پوشش محافظ در برابر خوردگی معیار مهمی برای طول عمر خطوط لوله و عملکرد ایمن آن است. در اروپا، برای ایالات متحده آمریکا و همه کشورهای بزرگی که خطوط لوله در آن ها کار گذاشته میشود، استانداردها و دستورالعملهای متعددی وجود دارد که خواص و عملکرد این پوششهای محافظ را مشخص می کند. مانند استاندارد DIN EN12068 (DIN استاندارد آلمانی می باشد)
برای انتخاب یک سیستم پوشش دهی مناسب و مقاوم در برابر خوردگی، مواردی مانند اندازه پروژه، امکان پذیری پاکسازی لوله ها و همچنین شرایط ویژه عملیاتی خطوط لوله باید در نظر گرفته شود و این موارد لزوماً به شدت به یکدیگر مرتبط هستند. این مقاله بر روی تجربیات ساخت نوارهای پلاستیکی سه لایه تمرکز می کند. این نوع پوشش ها با توجه به لایه های لاستیک بوتیل خود ادغام شونده، اکنون 30 سال است که عملکرد عالی خود را در پوشش های میدانی ثابت کرده اند.
مقدمه
به نقل از Derek Mortimore ، یکی از متخصصان پیشرو خوردگی در جهان، "خطوط لوله خراب نمی شوند، مگر این که ابتدا پوشش آن ها خراب شود". این نظریه توسط نظرسنجی بین المللی NACE ، بزرگترین سازمان خوردگی جهان، و بزرگراه فدرال ایالات متحده ، اداره ای که در سال 2002 ساخته شد، پشتیبانی می شود. سالانه بیش از 7 میلیارد دلار در ایالات متحده برای تعمیر هزینه های خوردگی خطوط لوله بایستی سرمایه گذاری شود.
مجموع هزینه های خوردگی در همه بخش ها بیش از 276 میلیارد دلار در سال است! بنابراین انتخاب سیستم محافظ در برابر خوردگی مناسب با دقت بالا الزامی می باشد.
تجربه و تاریخچه طولانی مدت مواد بازدارنده خوردگی در آلمان
بر اساس نیازهای مختلف در مکان های مختلف، سیستمهای پوششی متعددی در دهههای گذشته ، به طور مداوم توسعه و بهبود یافتهاند. برای دریافت دیدگاه مناسب از عملکرد سیستم های پوشش دهی مختلف، نگاهی به تجربه بلند مدت سیستم های پوشش میدانی خطوط لوله مورد استفاده در دوره های مختلف ساخت و ساز، مرجع خوبی خواهد بود.
E.ON Ruhrgas، تقریبا به عنوان بزرگترین توزیع کننده گاز طبیعی در اروپا، کار می کند. 12000 کیلومتر خطوط لوله گاز فشار قوی، بین سال های 1912 و 2006 ساخته شده اند. جدول 1 نمای کلی از پوشش های مشترک پایه را نشان می دهد. با توجه به پیشرفت تکنولوژی در طی سال های ساخت، برای این خطوط لوله از انواع مختلف سیستم های پوشش پایه استفاده شده است.
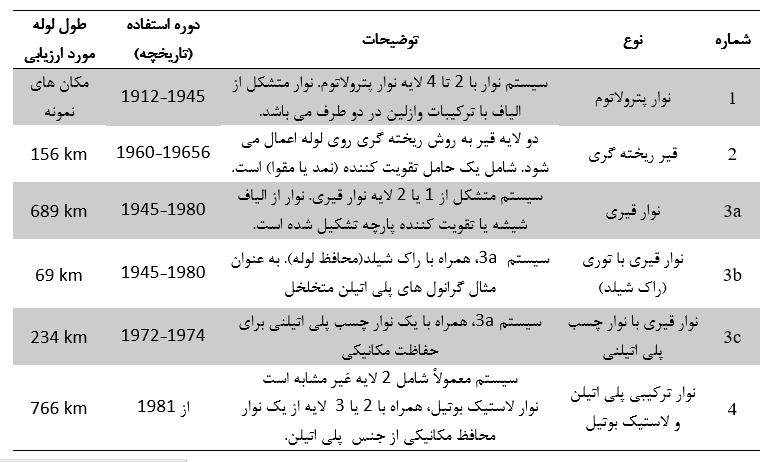
از نتایج روش های مختلف بررسی خطوط لوله که در دوره های مختلف ساخت و ساز برای خطوط لوله اعمال شده است، تفاوت های قابل توجهی در عملکرد حفاظت در برابر خوردگی پوشش مناطق اتصال وجود دارد.
* سیستمهای نوار پترولاتوم (که بین سالهای 1912 و 1945 مورد استفاده قرار گرفتند) به مرور زمان تخریب شده و در نتیجه مناطق بزرگ فلزی لوله بدون پوشش را در معرض محیط اطراف قرار می دهند، که در آن بازده حفاظت کاتدی ممکن است سوال برانگیز باشد. در این سیستم تداخل در سازه های مجاور باید در نظر گرفته شود.
* قیر ریخته گری شامل یک حامل تقویت کننده ، با احتمال چسبندگی ضعیف در بخش پایینی لوله ، علت کیفیت ضعیف این سیستم پوشش برای کاربرد میدانی را نشان می دهد. در این سیستم حفاظت کاتدی به طور موثر انجام می شود ولی از نظر فنی غیرقابل استفاده است. نرخ خوردگی ناچیز (یعنی بیش از 0.01 میلیمتر بر سطح) باید مورد انتظار باشد.
* سیستمهای نوار قیری با الیاف شیشه یا تقویت کننده پارچه ممکن است در طول زمان عیوب پوششی بزرگتری از خود نشان دهند که منجر به اثربخشی سوال برانگیز حفاظت کاتدی و همچنین چسبندگی ضعیف میشود. اما عموما تمایلی به محافظت از سطح فولاد در برابر جریان حفاظت کاتدی ندارند. اگر پلی اتیلن اضافی نوار به عنوان پوشش بیرونی اعمال شود، وضعیت به طور چشمگیری تغییر خواهد کرد. زیرا منجر به محافظت از جریان حفاظت کاتدی می شود؛ بنابراین نرخ خوردگی از نظر فنی غیر قابل چشم پوشی است (یعنی بیش از 0.01 میلی متر در سطح باید پیش بینی شود.)
* نوارهای ترکیبی پلی اتیلن/ لاستیک بوتیل دارای خواص حفاظتی عالی در برابر خوردگی هستند. این نوارها (که از سال 1981 سیستم پوشش مشترک میدانی ترجیحی برای خطوط لوله E.ON-Ruhrgas بوده اند) نه منافذ بیش از حد ، نه از دست دادن چسبندگی و نه کاهش استحکام نوار چسب را نشان می دهند. این ارزیابی بر اساس تجربه عملی در پروژه های خطوط لوله بیش از 25 سال است.
با جمع بندی این نتایج، توصیه می شود که سیستم های پوشش دهی مناطق اتصالات را با توجه به چسبندگی طولانی مدت و استحکام کششی آن ها انتخاب کنید. هر ترکیب افزودنی در سیستم پوشش دهی، به عنوان مثال، استفاده از موادی که از خطر آسیب های مکانیکی جلوگیری می کنند، که ممکن است منجر به محافظت از سطح فولادی لوله در برابر جریان حفاظت کاتدی شود، باید اجتناب شود.
الزامات عمومی برای پوشش های محافظ در برابر خوردگی:
الزامات عمومی مواد برای پوشش دهی خطوط لوله چیست؟
این مواد در طول عمر مفید خود باید تنش های مختلفی را تحمل کنند (جدول 2).
در حالی که پوششهای کارخانه ای برای رسیدن به حداکثر مقاومت مکانیکی متمرکز شدهاند، الزامات پوششهای میدانی بر روی کاربری آسان و تحملپذیری خطاهای اجرا و استفاده ، تحت شرایط متغیر آب و هوایی متمرکز است.
به دلیل تطبیق پذیری استفاده برای سیستم های پوشش میدانی، الزامات کلی برای همه مواد وجود ندارد. دستورالعمل های مربوطه DIN 30672 و EN 12068 برای مواد پوشش میدانی به سه کلاس تنش مکانیکی B،A و C و سه کلاس دمای عملیاتی( بالای 30 oC ، بالای 50 درجه سانتی گراد و - HT دماهای بالا ) به طور مجزا طبقه بندی می شوند. طبقه بندی این مواد مختلف با توجه به کلاس های تنش در جدول 4 اشاره شده است.
پوشش های میدانی نیازی به مقاومت مکانیکی مشابه پوشش های کارخانه ای ندارند. به ویژه مقاومت پارگی مواد پوشش (منظور پوشش میدانی) عمدتاً وابسته به دما هستند. برخی از منشاهای اصلی عیوب پوشش های لوله، مانند حمل و نقل و بارگیری نباید در نظر گرفته شوند. بنابراین، به دلیل استفاده بهتر در سیستم های میدانی، انتخاب مواد برای پوشش دهی اتصالات، که مقاومت مکانیکی کاهش یافته را نشان می دهند، بلامانع است. جداسازی توری محافظ لوله (راک شیلد) ممکن است برای جلوگیری از اعمال نیروهای برشی خاک محلی بر روی پوشش مناسب باشد.
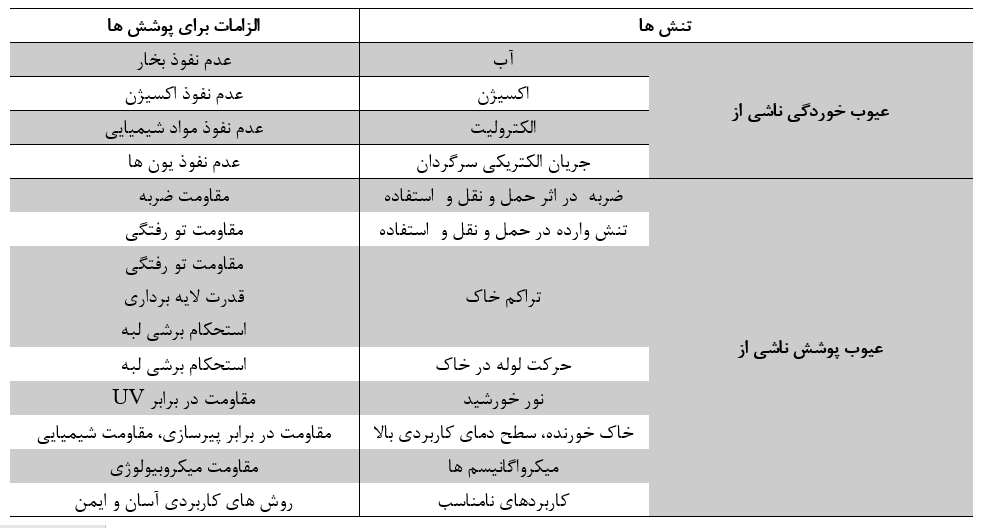
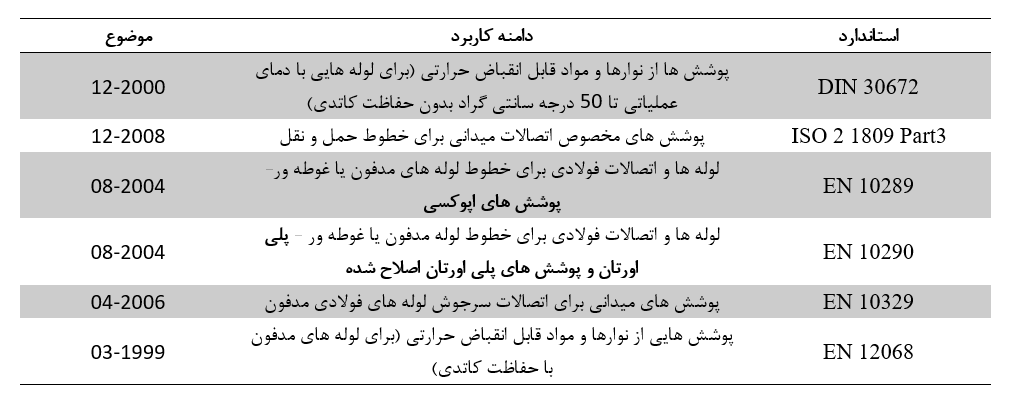
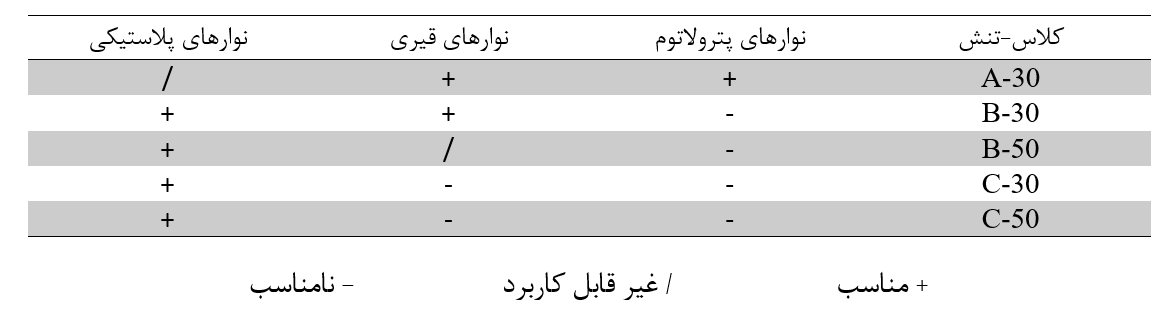
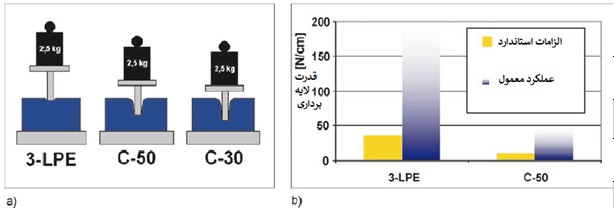
شکل1: a) ضخامت باقیمانده معمول پس از آزمون های فرورفتگی یک پوشش پلی اتیلن سه لایه در مقایسه با پوشش های نواری تنش کلاس C-50 و C-30 (در دمای 23 درجه سانتی گراد)
(b استحکام لایه برداری پوشش های کارخانه ای پلی اتیلن 3 لایه (DIN 30670) در مقایسه با پوشش های میدانی کلاسC 50 (EN 12068) در دمای 23 درجه سانتی گراد
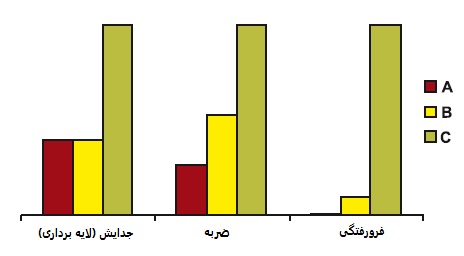
شکل 2: تفاوت در الزامات برای استحکام لایه برداری، مقاومت در برابر ضربه و مقاومت در برابر فرورفتگی در کلاس های تنش A، B و C بر اساس EN 12068
خواص فنی یک پوشش نوار محافظ در برابر خوردگی در مقالات و استانداردهای ملی و بین المللی مربوطه توضیح داده شده است. باید توجه داشت که استانداردهای ASTM که به طور مکرر مورد استفاده قرار میگیرند، حاوی روشهای آزمون مناسب برای تعیین یک خصوصیت هستند، اما آن ها نه معیارهای پذیرش را تعریف می کنند و نه همه ویژگی های یک پوشش نوار را یک جا ارزیابی می کنند.
در مقابل استانداردهای مواد مانند استاندارد اروپایی EN 12068 ، نه تنها نحوه تعیین خواص پوشش نوار مربوطه را توصیف میکنند، بلکه با مفهوم کلاسهای تنش، ابزار مناسبی برای طبقهبندی پوشش های نواری ارائه میدهند. کلاس های تنش مکانیکی A، B و C اساساً در مورد الزامات برای استحکام لایه برداری، مقاومت در برابر ضربه و مقاومت در برابر فرورفتگی متفاوت هستند. نسبت های مربوطه در شکل 2 نشان داده شده است.
هنگام انتخاب پوشش نوار محافظ در برابر خوردگی با توجه به کلاس های تنش باید در نظر گرفت که سطح عملکرد یک پوشش استاندارد کارخانه، به عنوان مثال پوشش پلی اتیلن سه لایه، از سطح عملکرد یک پوشش میدانی فراتر رود. همچنین مشخص است که برای پوشش های نواری با کلاس تنش دمایی بالاتر (50 به جای 30) همیشه نشان دهنده استحکام لایه برداری یا مقاومت در برابر فرورفتگی بالاتری است.
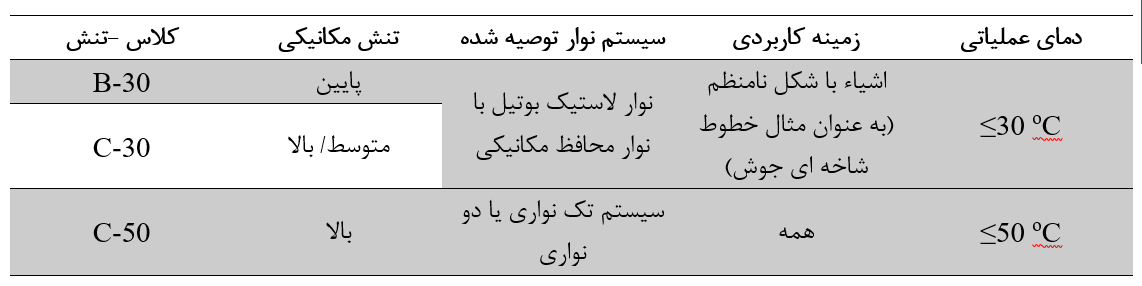
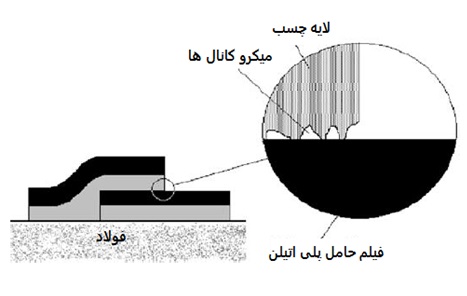
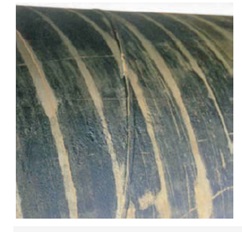
سیستم های نوار پلاستیکی:
در هر موردی که خطوط لوله با پوشش های نواری باید به تازگی نصب شوند یا به دلیل آسیب های خوردگی بازسازی شوند، فقط سیستم های نوار دولایه درگیر هستند. نگرش منفی نسبت به سیستمهای پوشش نواری که در بسیاری از کشورها مانند کشورهای عربی یافت میشود و منجر به تجربیات منفی بیست سال اخیر شده است از همین واقعیت نشأت میگیرد. دلایل اصلی شکست آن ها خواص مواد و ایرادات کلی سیستم پوشش دهی و همچنین روش های نامناسب استفاده است.
به خصوص برای نوارهای PVC (پلی وینیل کلراید) و پایه قیری، معایب ذاتی مواد از دلایل اصلی مردودی پوشش است. از آن جایی که PVC در اصل یک ماده نسبتا شکننده است، نوارهای PVC حاوی مقدار مشخصی از مواد افزودنی نرم کننده می باشند. در طول عمر پوشش لوله، این مواد نرمکننده از لایه حامل پخش شده و در بین سطح چسب-فولاد جمع میشوند ، که این امر منجر به شکنندگی لایه حامل و کاهش چسبندگی میشود. با توجه به این اثر، پس از گذشت سال ها، اغلب تنها بقایای جزئی نوار روی سطح لوله باقی میماند.
اگرچه نوارهای دو لایه بر پایه پلی اتیلن و لاستیک بوتیل معمولاً از چنین مشکلاتی برخوردار نیستند، اما آن ها نیز مردود شده اند. علت این موضوع را می توان عمدتاً با نامناسب بودن نوارهای دو لایه برای الزامات اولیه حفاظت در برابر خوردگی توضیح داد.
پوشش های محافظ در برابر خوردگی بایستی یک مقاومت اولیه در برابر خوردگی ایجاد کنند که این کار توسط پوشاندن سطح فلز با ماده ای که از متراکم شدن آب روی سطح جلوگیری می کند، انجام می شود. مواد مناسب ترکیبات پلاستیکی دائمی (پترولاتوم، لاستیک بوتیل) و همچنین ترکیبات سفت و سخت (پلی اورتان، رزین های اپوکسی) هستند. به عنوان عملکرد دوم، پوشش باید با جلوگیری از انتشار یا نفوذ آب و اکسیژن، سطح را آب بندی کند.
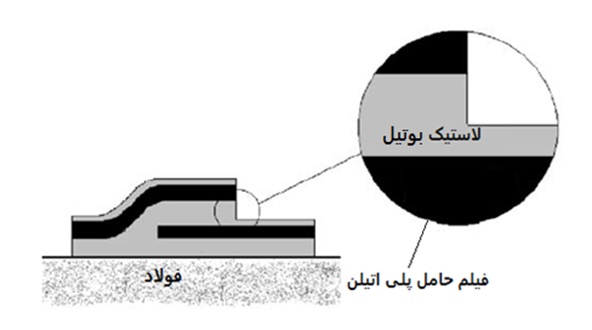

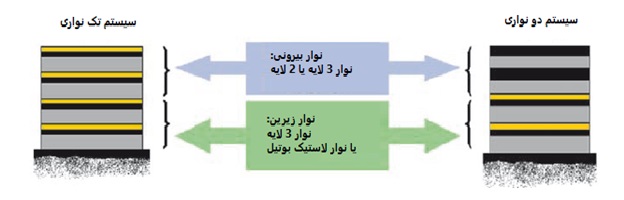
نوارهای دو لایه حاوی یک فیلم حامل هستند که تنها یک طرف آن با چسب پوشانده شده است. به دلیل این ساختار، آن ها می توانند حفاظت اولیه در برابر خوردگی را به خوبی نوارهای 3 لایه ایجاد کنند. زیرا چسبندگی به سطح فولاد، زمانی که سطح توسط رنگ پرایمر پشتیبانی می شود بهتر می شود. از سوی دیگر ویژگی آب بندی در نواحی هم پوشانی سیستم های نواری دو لایه نمی تواند به طور کامل از نفوذ عوامل خورنده جلوگیری کند.
در خطوط رابط باقی مانده بین لایه های یک سیستم نوار دو لایه، ممکن است میکرو حفره هایی وجود داشته باشد یا تشکیل شود، که بر اثر نفوذ احتمالی آب و اکسیژن (شکل 3) در نتیجه خوردگی مارپیچی (شکل 4) در بسیاری از خطوط لوله که در آن دو لایه نوار درگیر هستند، مشاهده می شود. این حالت به خصوص زمانی که تنها دو لایه نوار با هم پوشانی فقط 25 میلی متر یا کمتر استفاده شده باشد و از لایه چسب داغ پوشش داده شده روی نوار استفاده شده باشد، مشاهده می شود. در حالت دوم، لایه های چسب نازک قادر به پر کردن حفره های تشکیل شده در مناطق همپوشانی نیستند.(شکل 4)
نوار سه لایه خود ادغام شونده (خود ممزوج)
"خود ممزوج" به چه معناست؟
در نگاه اول، توصیه سیستم های نواری برای بازسازی یا ساخت و سازهای جدید پوشش های خط لوله ، زمانی که اقدامات نوسازی به دلیل خرابی سیستم نواری که در ابتدا روی سطح لوله اعمال شده بود ، آزار دهنده به نظر می رسد.
با این حال باید به وضوح بین نوارهای دو لایه و سه لایه خود ممزوج تمایز قائل شد. دومی حاوی یک فیلم حامل از پلی اتیلن با پایداری مطلوب است که از هر دو طرف با یک چسب لاستیک بوتیل پوشانده شده است. فیلمهای حامل از نوارهای سه لایه اکسترود شده با لایههای چسب میانی تولید میشوند و این اطمینان را میدهند که هیچ خط اتصال ریز مشخصی بین فیلم حامل و لایه چسب باقی نمیماند. هنگامی که نوارهای سه لایه به صورت مارپیچی به دور لوله پیچیده میشوند، لایههای چسب در مناطقی روی هم قرار میگیرند و پوششی از نوع آستر همگن را بدون هیچ گونه خط اتصال باقیمانده تشکیل میدهند (شکل 5).
فرایند خودآمیختگی و آب بندی یک سطح فولادی بدون هیچ حفره ای یک خصوصیت مهم لاستیک بوتیل است. از نقطه نظر فیزیکی ، لاستیک بوتیل بیشتر به صورت مایع وجود دارد تا جامد. مولکول ها در مناطق هم پوشانی از لایه ای به لایه دیگر مهاجرت می کنند و پس از یک دوره زمان مشخص، فصل مشترک اصلی لایه ها ناپدید می شود. (شکل 6)
پس از انتخاب لاستیک بوتیل و پلی اتیلن به عنوان پایه مواد، سوال در مورد مناسب ترین ساختار نوار مطرح شده است. سیستم های پوشش نواری برای توان بخشی خطوط لوله در هر صورت باید شامل حداقل دو لایه از یک نوار پلی اتیلنی سه لایه به همراه یک نوار لاستیک بوتیل باشد تا از یک نوار همگن با لایه تقریبا غیر قابل نفوذ در پوشش جدید استفاده شود.
این نوار خود ادغامشونده می تواند با چندین نوار تکمیلی و پوششهای آغازگر ترکیب شود تا حداکثر عملکرد محافظتی در برابر خوردگی را روی سطوح فولادی آمادهشده مختلف به دست آورد.
به عنوان حداقل نیاز، نوار زیرین یا نوار محافظ در برابر خوردگی باید همیشه ساختاری سه لایه با لایه های چسب لاستیک بوتیل در دو طرف یک فیلم حامل پلی اتیلن باشد و از یک نوار محافظ مکانیکی به عنوان یک نوار بیرونی پوشیده شده باشد. تجربه طولانی مدت نشان داده است که بهترین نتایج در حفاظت و چسبندگی به جای یک سیستم تک نواری از نوار سه لایه اکسترود شده به عنوان پوشش داخلی و خارجی حاصل می شود.
در میان این ساختارهای نوار 3 لایه، نوار نامتقارن ترجیح داده می شود، زیرا لایه چسب داخلی ضخیم با پر کردن بی نظمی های سطحی و حفره های احتمالی محافظت در برابر خوردگی را تضمین می کند. علاوه بر این، نوارهای ضد خوردگی نامتقارن پیشرفته ، ساختاری چهار لایه دارند که حاوی یک لایه اضافی بین فیلم حامل و چسب است. این لایه میانی از ترکیبی از لاستیک بوتیل و پلی اتیلن اکسترود می شود و بنابراین انتقال همگن از لاستیک بوتیل به پلی اتیلن را تضمین می کند. با توجه به فناوری تولید منحصر به فرد اکستروژن همزمان نوارهای سه لایه، اثر لایه لایه شدن شناخته شده (شکل 9) و از نفوذپذیری طولانی مدت بالقوه از طریق رابط بین فیلم حامل و چسب توسط ساختار نوار نشان داده شده در شکل 11 اجتناب می شود.
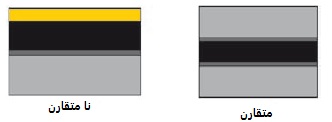
شکل 8: نمای مقطعی نوارهای سه لایه جلوگیری از خوردگی
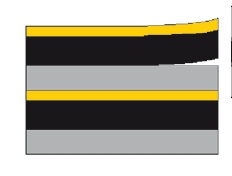
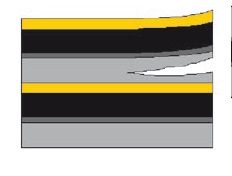
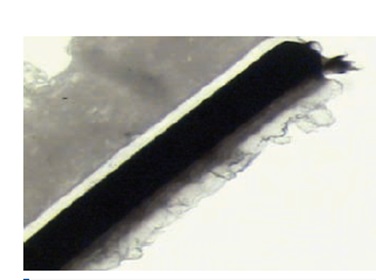