1. مقدمه
هدف اصلی تحقیق حاضر تعیین تأثیر سطوح بالای آلودگی نمکی بر روی سطوح لوله فولادی کربنی St3، ابزار برقی آماده شده، قبل از استفاده از دو روکش انقباض حرارتی «دو لایه» پرکاربرد برای استفاده در کاربردهای خط لوله زیر دریا است. کمک به دانش در صنعت پوشش خطوط لوله دریایی، در منطقه ای که داده های محدودی منتشر شده است، ارائه داده های معنادار، به شرکت های نفت و گاز، اپراتورها و تامین کنندگان مواد اجازه می دهد تا استانداردها و مشخصات طراحی و پردازش را با اطمینان بیشتری تنظیم کنند.
در حین لوله گذاری در دریا، طول لوله ها معمولاً 12.2 متر (40 فوت) و با یک لایه محافظ ضد خوردگی در کارخانه پوشش داده می شوند سپس به یکدیگر جوش داده می شوند تا خط لوله را تشکیل دهند. انتهای لوله که برای تسهیل در عملیات جوشکاری بدون پوشش هستند، با پوشش سرجوش میدانی (FJC) در حین لوله گذاری اعمال می شود. باید عنوان کرد که بر این اساس، یک خط لوله 100 کیلومتری احتمالاً بیش از 8000 درز میدانی خواهد داشت که در صورت عدم اعمال موثر پوشش سرجوش میدانی، هر یک از آن ها می تواند محل حمله خوردگی خارجی شدید باشد. کنترل شرایط در طی فرایند لوله گذاری همیشه آسان نیست و آماده سازی سطح نقاط سرجوش مهم است که در پروژه عملکرد قابل قبولی را بدون بحران ارائه دهد که این عدم آماده سازی منجر به هزینه های غیرضروری قابل توجهی، به خصوص با "نرخ های ساعتی" بالا مرتبط با لوله گذاری در دریا می شود.
طیف گسترده ای از انواع پوشش FJC موجود است که در ارتباط با سیستم حفاظت کاتدی خط لوله (CP) برای ارائه یک سیستم ضد خوردگی یا محصول طراحی شده برای محافظت عمری از خط لوله کار می کند. این مقاله مربوط به روکش های دولایه قابل انقباض حرارتی (HSS- Heat Shrink Sleeves) است که معمولاً برای پوشش دهی FJC خطوط لوله دریایی بتنی سنگین استفاده می شود، که روکش معمولاً با یک پلی اورتان جامد یا فوم پر می شود. پوشش های مشابه نیز گاهی اوقات بر روی خطوط غیر بتنی استفاده می شود.
HSS یک دسته پرکاربرد خط لوله FJC را تشکیل می دهد. در ساده ترین شکل خود، در مقایسه با جایگزین های پیچیده تر، نسبتاً سریع و آسان استفاده می شوند. سیستم های FJC نوع HSS می توانند گسترده باشند و به دو دسته تقسیم می شوند؛ روکش های انقباضی حرارتی 3 لایه (3LHSS) و روکش های انقباضی حرارتی 2 لایه (2LHSS) .
این مقاله به طور خاص به اثر نمک های محلول بر روی سطح فلز آماده شده قبل از استفاده انواع 2LHSS مربوط می شود، که ماستیک/چسب مستقیماً به سطح بدون پرایمر می چسبد.
عملکرد همه پوشش ها به شرایط بستری که روی آن اعمال می شود بستگی دارد، ویژگی های سطح و تمیزی دو عامل اساسی هستند. این امر به ویژه برای پوششهایی با کارایی بالا که آلودگی سطح توسط نمکهای محلول تأثیر قابلتوجهی بر چسبندگی طولانیمدت آنها دارد، حائز اهمیت است. مقدار آلودگی نمک محلول در آماده سازی سطوح لوله، توسط گریت بلاست، قبل از استفاده از سیستم های پوششی با کارایی بالا، معمولاً در سال های اخیر 20 میلی گرم بر متر مربع تعیین شده است و برای محافظه کارانه بودن، برخی از شرکت های نفت و گاز حداکثر سخت گیری در الزامات را تا 10 میلی گرم بر متر مربع مشخص می کنند.
اولین لایه از یک سیستم روکش انقباض حرارتی 3 لایه (3LHSS) (نوع 2B/2C) (ISO-21809-3:2008,2008)، یک اپوکسی مایع دو جزئی می باشد. برخلاف 3LHSS، سیستم روکش انقباض حرارتی 2 لایه (2LHSS) (نوع 2A) (ISO-21809-3:2008,2008)، از لایه اول اپوکسی مایع استفاده نمی کند، بلکه یک «ماستیک» یا لایه "مذاب داغ" مستقیماً روی سطح فلز لوله قرار می گیرد. حداکثر سطح قابل قبول آلودگی نمک روی سطوح فلزی آماده شده قبل از استفاده از 2LHSS موضوع بحث و تمرکز این مقاله می باشد.
استاندارد ISO 21809-3 برای پوشش مناطق سرجوش میدانی می باشد و برای اولین بار در سال 2008 منتشر شد، بخش 9.1.2.2 بیان می کند که اندازه گیری مقدار نمک های محلول روی سطح فولاد برای انواع پوشش های 1A، 1B، 1C ، 1D و '7 ضروری نیست. سیستم 2A بر پایه پلی اتیلن مواد قابل انقباض حرارتی است [بدون اپوکسی مایع]. در سال 2011 تمرین توصیه شده DNV-RP-F102 برای پوشش سرجوش میدانی مطابق با ISO 21809-3 با ادغام دستورالعمل راهنمایی زیر برای خط 2LHSS هم راستا شد.
شرایط غیر قطعی ممکن است دلیل بر این باشد که برخی از اپراتورها به تعیین حداکثر سطوح آلودگی نمک 30 یا 50 میلی گرم بر متر مربع برای 2LHSS ادامه می دهند. این مطالعه شواهدی مبنی بر بی اهمیت بودن سطوح بالاتر آلودگی نمک بر عملکرد دو مورد از رایج ترین سیستم های 2LHSS مورد استفاده برای خطوط لوله دریایی در سطح جهان در دهه گذشته ارائه می دهد. مشخص شد که سطوح آلودگی نمک تا 120 میلی گرم بر متر مربع هیچ تاثیری بر عملکرد لایه برداری پس از تسریع پیرسازی با غوطه وری در آب داغ ندارد. علاوه بر این، آماده سازی برای جوشکاری و استفاده از آب در طی روش های آزمون اولتراسونیک قبل از پوشش سرجوش میدانی معمولاً سطح آلودگی نمک را به زیر 50 میلی گرم بر متر مربع کاهش می دهد و عمل حذف آلودگی نمک را غیر ضروری می داند.
در سالهای اخیر یک روند صنعتی به سمت استفاده از روکش های انقباضی حرارتی سه لایه به همراه پر کردن وجود داشته است و این مقاله، با برجسته کردن ناچیز بودن اثر آلودگی نمک سطحی ، ممکن است اعتماد بیشتری به سیستم مقرون به صرفهتر 2LHSS ایجاد کند.
2. روش آزمون
خطر احتمالی مردودی پوشش به دلیل پاک سازی ضعیف آلودگی سطح با آزمایش چسبندگی بین پوشش و زیرلایه فولادی که پوشش به آن چسبیده است، پس از یک دوره غوطه وری در آب داغ ارزیابی شد. طبق استاندارد ISO 21809-3 "Annex I" انجام این آزمون به 28 روز غوطه وری در حداکثر دمای عملیاتی نیاز دارد. برای این مطالعه، برای ایجاد یک وضعیت شدید، حلقههای آزمایشی (لوله های کوچک) با غوطهوری در آب در دمای مشخص شده در HSS بالای 65 درجه سانتیگراد برای بیش از دو برابر دوره تعیینشده در معرض پیرسازی تسریعشده قرار گرفتند( ISO_21809-3:2008, 2008).
2HSS مورد آزمون قرار گرفت: یکی از پوشش هایی که به طور گسترده در شرایط تنش مکانیکی متوسط استفاده می شود ، دارای یک چسب "هیبرید" ماستیک با مقاومت برشی بالا که حاوی نسبت قابل توجهی از پلی پروپیلن آمورف مخلوط با مواد چسبنده و EVA است، که به عنوان " نوع A "شناخته می شود. نوع دوم که به عنوان "نوع B" نامیده می شود، به طور گسترده در مواردی استفاده می شود که توسط یک لایه "پرکننده" پوشانده شده است، که معمولاً از فوم پلی اورتان یا الاستومر پلی اورتان جامد تشکیل شده است. به عنوان مثال، روش طراحی معمولی برای خطوط لوله با پوشش بتنی. نوع B دارای استحکام متوسط تری نسبت به نوع سنتی ماستیک نوع A بود که حاوی درصد قابل توجهی لاستیک بوتیل با آسفالت، عوامل فعال کننده و رزین های چسبنده می باشد.
برای تعیین نحوه اعمال آلودگی نمکی بدون ایجاد زنگ زدگی، یک مطالعه کوچک بر روی بستر فولادی انجام شد. پس از آزمایشهای متعدد، غیرممکن بود که زنگزدگی قابل مشاهده روی سطح لوله ایجاد نشود. میزان زنگ زدگی با حرارت دادن لوله بلافاصله پس از استفاده از محلول نمک به حداقل رسید.
برای دست یابی به طیف وسیعی از آلودگی نمکی کم تا زیاد نزدیک به سطوح هدف، یک مطالعه اولیه انجام شد. روش انتخاب شده با استفاده از یک روش ساده و عملی، نتایج ثابتی را ارائه کرد. یک محلول نمک دریای اشباع تهیه شد (با ارائه یک غلظت کنترل شده از نمک). سپس این محلول با آب آشامیدنی با نسبتهای مختلف رقیق شد و بر روی سطح لوله اسپری شد. حلال اضافی تبخیر شد و مقدار کنترل شده ای از نمک را باقی گذاشت.
میزان نمک روی سطح لوله پس از استفاده از محلول نمک آماده شده با استفاده از دستگاه Elcometer SCM 130 اندازه گیری شد، ابزاری که معمولاً برای این منظور در صنعت پوشش دریایی استفاده می شود. این آزمایش شامل حل کردن نمک محلول روی سطح لوله با استفاده از یک کاغذ صافی آزمایشگاهی آغشته به 1.6 میلی لیتر آب غیر معدنی و ارزیابی رسانایی کاغذ پس از یک دوره استفاده می باشد.
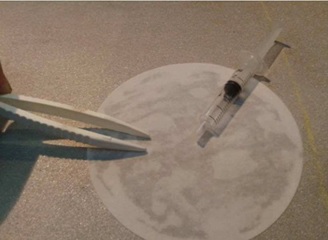
شکل 1: کاغذ صافی با 1.6 میلی لیتر آب غیر معدنی اعمال شده است
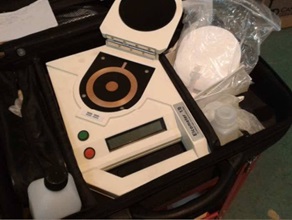
شکل 2 : دستگاه سنجش آلودگی نمک

شکل 3: روش پاشش نمک
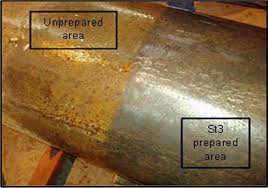
شکل 4: اعمال محلول نمک روی سطح آماده شده
لوله های آزمایشی به طول 1 متر از لوله فولادی کربنی با قطر 12 اینچ با ضخامت دیواره 25 میلی متر تهیه شدند. لوله ها قبل از استفاده به مدت تقریبی 2 سال در هوای آزاد نگهداری می شدند و سطح خوردگی متوسطی داشتند. سطوح لوله قبل از اعمال نمک کنترل شده توسط ابزار برقی مطابق با استاندارد ISO 8501-1 آماده سازی شدند. منبع نمک 100% نمک دریای بومی حل شده در آب آشامیدنی بود. برای نمونه نمک «صفر» آب مقطر با گرید خودرو روی سطح لوله پاشیده شد، که منجر به قرائت نمک سطحی واقعی 4 میلی گرم بر متر مربع شد (نمک سطح باقی مانده موجود که به طور کامل در آب مقطر حذف نشده بود).
جدول زیر خلاصه ای از سطوح نمک سطحی به دست آمده، نسبت به مقادیر هدف، اندازه گیری شده در چهار نقطه شعاعی سطح لوله (a، b، c و d ) را ارائه می دهد.
محلول نمک اشباع کاربردی | قرائت نمک سطحی در 4 مکان (mg/m2) a | قرائت نمک سطحی در 4 مکان (mg/m2) b | قرائت نمک سطحی در 4 مکان (mg/m2) c | قرائت نمک سطحی در 4 مکان (mg/m2) d | میانگین خوانش واقعی (mg/m2) | مقدار هدف (mg/m2) |
آب غیر معدنی | 5 | 4 | 4 | 4 | 4 | 0≈ |
0.5 % (5ml/L) | 28 | 33 | 35 | 33 | 32 | 20≈ |
1.25 % (12.5ml/L) | 65 | 64 | 71 | 55 | 64 | 50≈ |
2.5 % (25ml/L) | 143 | 136 | 127 | 141 | 129 | 100≈ |
نمونه های HSS و امکانات برای استفاده آن ها، برای حصول اطمینان از این که برنامه مطابق با الزامات مشخص شده است و به طور مداوم کنترل می شود ، توسط سازنده HSS ارائه شده است.
لازم به ذکر است که در عمل در طی فرآیند پوشش دهی لوله، تمام طول لوله تا یک زبری سطح و تمیزی سطح مشخصی با گریت بلاست انجام می شود تا مشخصات زبری سطح مورد نیاز برای "پوشش اصلی" لوله، که معمولاً 3LPE ( پلی اتیلن سه لایه) یا 3LPP (پلی پروپیلن سه لایه) می باشد را فراهم کند؛ در هر دو مورد داشتن یک لایه اول FBE[Fusion bonded epoxy] که نیاز به یک سطح تمیز و ناهموار دارد، الزامی است. انتهای لولهها، که به عنوان «برشها» شناخته میشوند، بدون پوشش باقی میمانند و ممکن است بدون محافظت باقی بمانند یا دارای محافظ در برابر خوردگی موقت مانند لاک یا کلاهک پلاستیکی انتهایی یا هر دو باشند.
لولههای مورد استفاده در این مطالعه فاقد پوشش اصلی بوده و گریت بلاست نشده بودند. سطح پس از خروج از کارخانه لوله به طور کامل تمیز نشده بود و تقریباً دو سال در معرض فضای باز قرار داشت. لوله ها طبق استاندارد St3 با ابزار برقی تمیز شدند و سطح لوله ها نسبتاً صاف و با درجه های مختلفی از خوردگی سطح باقی ماندند. این یک سناریوی «بدترین حالت» نسبت به وضعیت تولید در نظر گرفته شد.
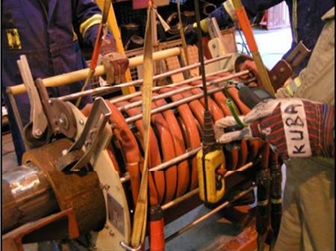
شکل5 : گرمای القایی لوله
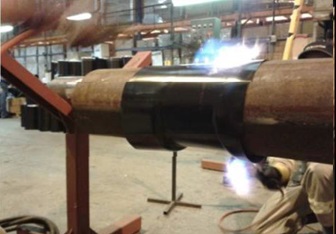
شکل 6: انقباض HSS با مشعل پروپان
روکش های انقباض حرارتی بر روی لوله های از پیش آلوده به دنبال روش های کاربردی توصیه شده توسط تامین کنندگان اعمال شد. پیش گرمایش لوله با گرمایش القایی با استفاده از یک مشعل پروپان بود. این مشعل، گرمایش یکنواخت و ثابت را فراهم کرد و از انقباض مرتبط با پیش گرمایش مشعل پروپان، که ممکن بود از یکنواختی غلظت نمک تأثیر بگیرد، جلوگیری کرد.
قبل از تسریع پیرسازی، به عنوان نمونه اولیه ، آزمایش لایه برداری بر روی هر نمونه HSS انجام شد. این کار بر روی برشها، در کنار لوله های آزمایش نمونه، با استفاده از روش لایهبرداری دستی انجام شد (شکل 9 را ببینید).
نمونههای لوله، با اعمال 2LHSS، به طول 150 میلیمتر (6 اینچ) برش داده شدند و فولاد در معرض دو سر هر لوله با چسب اپوکسی پوشش داده شد تا از نفوذ آب به زیر روکش ها در انتهای بریده شده جلوگیری شود. حلقههای آزمایشی مطابق با ضمیمه 1 استاندارد ISO 21809-3 با غوطهوری در آب در دمای 65 درجه سانتیگراد تحت پیرسازی تسریعشده قرار گرفتند، اما مدت زمان آن تا 60 روز دو برابر شد تا شرایط تست شدیدتری ایجاد شود. دمای مخزن آب به صورت ترموستاتیک با حداکثر تغییر 3 ± درجه سانتی گراد کنترل شد. غوطه ور شدن در آب به عنوان یک روش معمول برای تسریع نگرانی های "مردودی چسب" شناخته شده است.
غوطه وری در آب گرم توسط یک آزمایشگاه مستقل معتبر و با استفاده از یک مخزن غوطه وری بزرگ بر اساس ضمیمه 1 استاندارد ISO 21809-3 انجام شد، اما با غوطه وری 60 روزه (دوبرابر مدت زمان مشخص شده) و به دنبال آن تست چسبندگی لایه برداری در دمای محیط کنترل شده انجام شد.
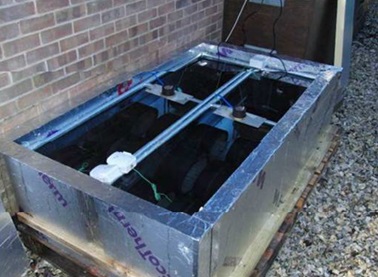
شکل 7: مخزن غوطه وری آب با هیتر و پروانه های همزن
1.2. استحکام لایه برداری نمونه های پیرسازی شده
ارزیابی بر روی نحوه مردود شدن در طی آزمون لایه برداری انجام شد. افزایش درصد «حالت جدایش سطحی» در مقایسه با «حالت جدایش منسجم» که نشاندهنده نگرانی ناشی از آلودگی سطحی ناشی از کاهش استحکام پیوند فولاد و ماستیک سطح است.
سرعت لایه برداری عامل مهمی برای چسب های نوع ماستیک مانند 2LHSS است. تغییر سرعت لایه برداری نه تنها بر استحکام لایه برداری تأثیر می گذارد، بلکه می تواند روی حالت جدایش، یعنی حالت سطحی یا منسجم نیز تأثیر بگذارد. برای اطمینان از یکنواختی، از یک دستگاه نیروسنج لایه بردار پرتابل و خودکار برای آزمون نمونه ها در مرزهای غلظت نمک بالا و پایین، با استفاده از سرعت 10 میلی متر در دقیقه مشخص شده در استاندارد های ISO 21809-3 و DNV-RP-F102 ، استفاده شد. آزمایش دستی با استفاده از نیروی اعمال شده معادل نیروی ثبت شده در طول آزمایش خودکار، با هدف تقریبی همان سرعت لایه برداری انجام شد.
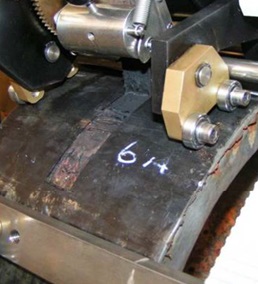
شکل 8: دستگاه خودکار لایه بردار در سرعت 10mm/min
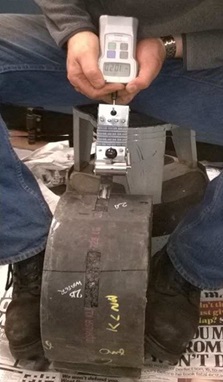
شکل 9: آزمون لایه برداری دستی با استفاده از نیروی کنترل شده
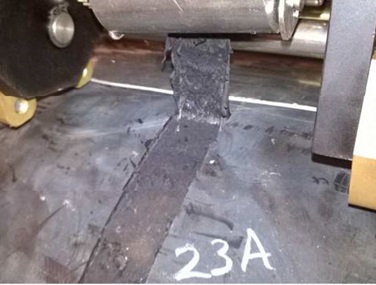
شکل 10 : نوع A HSS با بالاترین سطح نمک پس از 60 روز غوطه وری در آب در دمای 65 درجه سانتی گراد
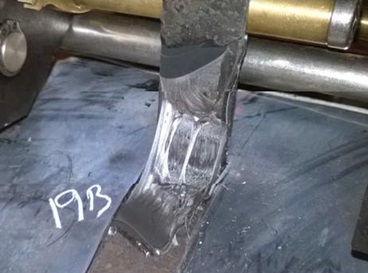
شکل 11: نوع B HSS با بالاترین سطح نمک پس از 60 روز غوطه وری در آب در دمای 65 درجه سانتی گراد
3. نتایج
مشاهدات اولیه پس از غوطه وری در آب داغ
پس از دوره غوطه وری 60 روزه در آب داغ در دمای 65 درجه سانتی گراد، لوله های آزمایش در یک محیط آزمایشگاهی کنترل شده به مدت 48 ساعت آماده شدند. مشاهدات زیر ذکر شد:
شکل 12 : ورود آب
شکل 12 : خزش / ازدیاد طول HSS
تمام نمونه های HSS تقریباً 3 تا 4 میلی متر در هر انتهای حلقه لوله کشیده شده بودند. نمونه های 1، 2، 3، 4 و 23 دارای نفوذ آب بودند که چسب به طور کامل سطح لوله را پوشش نداده بود. در برخی موارد، «نهر های» آب بین «دانههای» چسب وجود داشت.
مروری بر نتایج آزمایش لایه برداری
جدول 2 مقایسه بصری حالت جدایش لایه برداری معمولی را برای هر نمونه لوله آزمایش شده ارائه می دهد و شکل 12 قالب بندی اعداد جدول را نشان می دهد. چهار سطح آلودگی نمک به صورت ستونهای عمودی نشان داده شدهاند و دو نوع HSS با رنگهای مختلف بهصورت افقی از هم جدا شدهاند، با سه نمونه لوله در غلظت نمکی و 3 آزمون لایه برداری در هر نمونه لوله انجام شده است. حاشیه های قرمز نشان دهنده نمونه های لوله ای است که با استفاده از دستگاه تست لایه برداری خودکار آزمایش شده اند.
با استفاده از دستگاه لایه بردار خودکار، اندازه گیری ها از نمونه های آزمایشی با بالاترین و کمترین غلظت نمک با سرعت 10 میلی متر در دقیقه انجام شد. استحکام لایه برداری تقریباً 5 نیوتن بر میلی متر برای HSS نوع A و تقریباً 2 نیوتن بر میلی متر برای HSS نوع B بدون توجه به درجه آلودگی نمک باقی مانده بود.{ HSS نوع A لوله 3، با آلودگی نمک باقی مانده کم، و لوله 19 با آلودگی نمک باقی مانده بالا همراه است، HSS نوع B لوله با آلودگی نمک باقی مانده کم و لوله با آلودگی نمک باقی مانده بالا همراه است. }
شکل 12: کلید نتایج آزمایش لایه برداری (جدول 3 را ببینید)
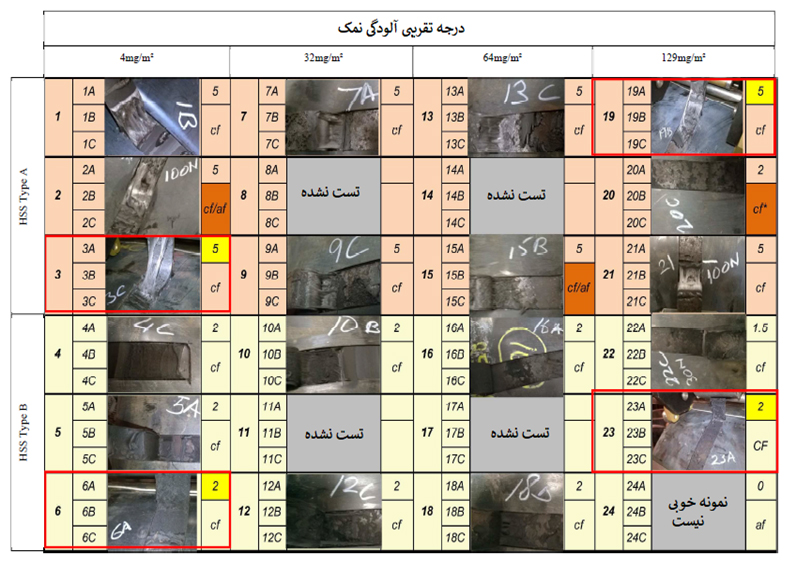
جدول 2: مروری بر نتایج آزمایش لایه برداری که نیروی لایه برداری و نحوه جدایش را نشان می دهد
4. بحث
1.4. بررسی نتایج آزمون
جدول 2 یک نمای کلی از رابطه بین میزان اعمال آلودگی نمک باقی مانده روی سطح و عملکرد استحکام لایه لایه شدن پس از غوطه وری در آب را ارائه می دهد.
1.1.4 ارتباط بین آلودگی نمک شبیه سازی شده و کارایی
هیچ ارتباط قابل توجهی بین قدرت لایه برداری یا حالت جدایش بین نمونه های با سطح آلودگی نمک بالا و نمونه هایی با سطوح آلودگی نمک کم مشاهده نشد. برخی تفاوتهای جزئی بین نتایج در هر نمونه مشاهده شد، اما این به احتمال وجود متغیرهای کنترلنشده که در فرآیند اعمال دستی ذاتی بودند نسبت داده شد.
2.1.4. اثر غوطه وری در آب
تنها تفاوت قابل توجه بین نمونههای شاهد (قبل از غوطهوری در آب) و نمونههای بعد از غوطهوری در آب، در عملکرد لایهبرداری HSS نوع A بود، این مورد هنگام لایهبرداری دستی اشاره شد که تمایل به درجه بیشتری از حالت جدایش سطحی وجود دارد. هنگام استفاده از دستگاه لایه بردار، مقدار میانگین مقاومت لایه برداری 5N/mm ثبت شده است. این پدیده به طور ویژه در نمونه شماره 20 مشهود بود، با نیروی اعمالی دستی بیشتر از 2N/mm ، ترکیبی از حالت جدایش سطحی و منسجم رخ داد. اما با نیروی کششی دستی کمتر از 2N/mm ، حالت جدایش منسجم رخ داد. (سرعت لایه برداری کمتر منجر به نیروی کمتر و حالت جدایش 100٪ منسجم شد).
یک فرضیه احتمالی برای این امر این است که یک تغییر در تمایل ماده ویسکوالاستیک به سمت کشسانی بیشتر و چسبندگی کمتر وجود دارد که منجر به آستانه سرعت پایینتر در انتقال حالت جدایش منسجم / سطحی میشود. برخی از افزودنیها / کسریها با وزن مولکولی کم ممکن است در طی فرآیند پیرسازی در آب داغ یا در اثر پیرسازی پلیمرهای اجزا ، از بین رفته باشند که منجر به چسبندگی کمتر و خاصیت چسب «سفتتر» میشود. این فرض با ظاهر این نمونه در حین لایه برداری تأیید شد. ممکن است این نمونه فردی نسبت به نمونه های دیگر در مجاورت یک شرایط اعمال حرارت با آب داغ قرار داشته باشد و این منجر به تاریخچه پیرسازی حرارتی بیشتر شده است.
لازم به ذکر است که الزام ISO 21809-3 برای حداقل استحکام لایه برداری 1N/mm برای این نوع روکش حرارتی می باشد. بنابراین، این به عنوان یک نگرانی برای عملکرد محصول در بازار در نظر گرفته نمی شود، بلکه یک مشاهده فقط مربوط به مطالعه آزمایشی حاضر است.
3.1.4. آماده سازی سطح لوله
سازندگان روکش انقباض حرارتی توصیه می کنند که HSS دو لایه باید بر روی یک سطح آماده شده با گریت بلاست اعمال شود، اما آن ها می پذیرند که سطح تمیز شده با ابزار برقی از استاندارد St3 ممکن است قابل قبول باشد. در عمل، 2LHSS معمولاً بر روی سطح تمیز شده با ابزار برقی St3 اعمال میشود، زیرا این امکان استفاده سریع را فراهم میکند و ماستیکهای مورد استفاده اجازه میدهند حداقل عملکرد مورد نیاز را بدون متحمل شدن زمان و هزینه اضافی مورد نیاز برای گریت بلاست به دست آورند.
آلودگی نمک محلول شبیه سازی شده از نمک دریایی خالص موجود در بازار ("100٪ نمک دریا") ایجاد شد. در نظر گرفته میشود که این رایجترین نوع نمک موجود در سطوح لوله فولادی با آماده سازی ضعیف است که معمولاً ممکن است در معرض یک محیط دریایی در محوطه پوشش لوله، محوطه ذخیرهسازی لوله و یا در حین حمل و نقل قرار گرفته باشد. این نوع نمک عمدتاً از سدیم کلرید (NaCl) تشکیل شده است. گفته می شود که اثر سولفات ها کمتر شایع می باشد و تأثیر کمتری بر چسبندگی پوشش دارد.
4.1.4. ناهنجاری در یافته ها
برخی ناهنجاری ها در نمونه ها مشاهده شد، مانند نمونه های 1، 2، 3، 4، 23 و 24، که در آن درجه ای از نفوذ آب رخ داده بود، ظاهراً به دلیل پوشش اولیه ضعیف (خیس شدن) بستر توسط چسب، به عنوان مثال، می تواند مربوط به یک خطای فرآیند در استفاده باشد. نمونههای 1، 2، 3 و 4 به عنوان چهار نمونه اول استفاده شده بودند و ممکن است مشکلی در راهاندازی تجهیزات گرمایش القایی وجود داشته باشد، یا احتمالاً به دلیل اعمال روکش ها روی لوله پوشش داده شده به نمونه های لوله بدون پوشش توسط پرسنل اجرا کننده باشد.
جنبه های زیر نیز ممکن است باعث ایجاد تغییراتی در کیفیت کاربرد HSS شود:
a) توزیع ناجور گرما ، زیرا سیم پیچ القایی باید در دو مرحله اعمال شود و لوله به میزان 90 درجه بین هر مرحله بچرخد (کنترل مستقل مدت زمان گرمایش القایی برای هر لوله با اندازه گیری دمای سطح به صورت دستی).
b) روکش های انقباض حرارتی معمولاً روی خط لوله پوشش داده شده با برش مشترک مناطق سرجوش میدانی اعمال می شوند.
پوشش اصلی لوله معمولاً به دلیل انقباض از طرفین HSS حمایت می کند و عدم وجود پوشش اصلی باعث می شود که اپراتورهای اعمال کننده HSS با احتیاط بیشتری نسبت به حالت عادی از HSS استفاده کنند تا از جمع شدن بیش از حد HSS جلوگیری شود.
2.4. حفاظت در برابر خوردگی خارجی خطوط لوله دریایی
بهینه سازی پوشش های خطوط لوله در ارتباط با حفاظت کاتدی به عنوان وسیله ای برای محافظت از خطوط لوله در برابر خوردگی، هدف دائمی اپراتورهای نفتی است. خطوط لوله غوطهور را میتوان تنها با حفاظت کاتدی و بدون استفاده از هیچ پوشش محافظی روی سطح فولاد کربنی بدون پوشش محافظت کرد. این مورد در خطوط لوله اولیه در خلیج Guinea اعمال شد، که در آن خطوط جریان کوتاه در ابتدا بدون پوشش یا حفاظت کاتدی نصب شدند و سپس آندهای روی (Zn) فدا شونده با کابلهای الکتریکی متصل شدند که در جلوگیری از خوردگی مؤثر بود. ترکیبی از پوشش لوله و حفاظت کاتدی اکنون به طور سیستماتیک برای محافظت از خطوط جریان و خطوط انتقال استفاده می شود زیرا پوشش دهی، ظرفیت مورد نیاز سیستم CP را کاهش می دهد. بنابراین، پوشش دهی، حفاظت از خوردگی عمومی خط لوله را فراهم میکند و اتصال آندهای فدا شونده (که عمدتاً از آلومینیوم تشکیل شدهاند) در فواصل زمانی منظم، از مناطق بدون پوشش موجود در برابر آسیب پوشش یا مکان هایی که پوشش دهی امکانپذیر نیست، محافظت میکند. جرم آند و فاصله در امتداد خط لوله برای محافظت از خط لوله ، بر اساس یک فرضیه محافظه کارانه از جمله در نظر گرفتن ضریب شکست پوشش برای نوع پوشش مورد استفاده، در طول عمر خط لوله طراحی شده است. استاندارد DNV RP F103 دستورالعمل ها و تمرین های توصیه شده را برای طراحی سیستم های CP ارائه می دهد. تا زمانی که پوشش به فولاد چسبیده باشد (یعنی به هیچ وجه جدا نشود) و حفاظت کاتدی به درستی اعمال، نظارت و نگهداری شود، نباید خطر خوردگی وجود داشته باشد. در صورت آسیب به HSS یا حذف نسبی HSS، ممکن است مقداری حفاظت کاتدی رخ دهد، این می تواند یک نگرانی جدی در مورد خطوط لوله خشکی باشد که در آن حفاظت کاتدی ممکن است کارآمد نباشد و در آن حفره های خوردگی موضعی ایجاد شود. با این حال، با توجه به خطوط لوله دریایی (جایی که آب دریا اجازه انتقال جریان الکتریکی کارآمد را می دهد)، با مطالعات خاص پروژه به این نتیجه رسیده اند که اثر پوشش بر اساس پیکربندی HSS و جریان درگیر قابل توجه نبوده و خطوط لوله به طور موثر محافظت می شوند.
3.4. آشنایی با لایه برداری ماستیک ها
برای دستیابی به چسبندگی ماستیک، "چسب" مورد نیاز است. چسبندگی خاصیت یک ماده چسبنده است که به موجب آن تماس لحظه ای ماده با یک جامد بلافاصله با مقاومت در برابر هرگونه تلاش برای جداسازی همراه می شود. رطوبت پوشش معمول سطح پروفیل لوله را توسط چسب ایجاد می کند و در واقع رطوبت بستر باعث پوشش خود به خودی می شود. ممکن است تصور شود که مرطوب شدن یک نیاز ضروری برای اتصال خوب چسب است. با این حال، این امر لزوماً در مورد چسب های بر پایه لاستیک (چسب های پایه آلی) صدق نمی کند زیرا سطح جذب یا چسبندگی بالا می تواند منجر به خیس شدن تدریجی بستر به دلیل جریان ویسکوز تدریجی شود. در مورد سیستم 2LHSS، چسبندگی با پیش گرم کردن بستر و گرم کردن روکش افزایش می یابد.
در معادله استفان، چسبندگی بین دو صفحه ایجاد شده توسط یک سیال نیوتنی در یک زمان معین، متناسب با ویسکوزیته سیال و معکوس با مجذور جداسازی است. چسب های پلیمری مورد استفاده با 2LHSS رفتار ویسکوالاستیک پیچیده ای دارند. با این حال، اصل گرم کردن سطح لوله فولادی آماده شده (پیش گرمایش) سطح بالایی از چسبندگی را فراهم می کند و ویسکوزیته چسب را کاهش می دهد تا بستر فولادی را خیس کند و در نتیجه چسبندگی سطحی را بهبود می بخشد. ویسکوزیته چسب با سرد شدن افزایش می یابد و استحکام پیوند را با همان اصل معادله استفان افزایش می دهد.
در مورد 2LHSS، ترکیب لایه چسب معمولاً ترکیبی از آسفالت و لاستیک بوتیل ولکانیزه نشده با سایر افزودنی ها و محرک های چسبندگی است. با این حال، اخیراً، ترکیبی از پلی پروپیلن آمورف با EVA و چسبنده ها (اغلب چسب های هیبریدی نامیده می شوند) به بازار آمده اند که عملکرد دمایی بالاتر و استحکام بالاتری را ارائه می دهند. در هر دو مورد ذکر شده، مواد را می توان به عنوان "ترموپلاستیک" در نظر گرفت، زیرا در هنگام گرم شدن نرم و ذوب می شوند، "تر شدن" زیرلایه توسط چسب را بهبود می بخشد و در طی سرد شدن با سخت شدن و تقویت چسب همراه است.
بیشتر پلیمرها درجاتی از رفتار ویسکوالاستیک را نشان می دهند. نسبت و میزان اجزای تغییر شکل یافته چسبناک و الاستیک به نوع پلیمر و ترکیب بستگی دارد. چسبهای نوع ماستیک تأکید زیادی بر اجزای ویسکوز دارند و به چسب اجازه میدهند تا به راحتی بستر را خیس کند و تغییر شکل را در طی استفاده و عمر مفید داشته باشد در حالی که دارای مقداری استحکام الاستیک برای ارائه عملکرد مکانیکی مورد نیاز است.
مدل نشان داده شده در شکل 15 درک مفهوم ویسکوالاستیک را ارائه می دهد. نیروی لایه برداری اندازه گیری شده به سرعت افزایش طول بستگی دارد. نمودار مدل Voight را نشان می دهد که در آن تنش حاصل در سرعت معین حاصل مجموع تنش فنری و تنش دشپات است. ویژگی ذاتی ماده مورد آزمایش، نسبت تنش منتسب به "الاستیک" (فنر) و جریان ویسکوز/ خزش (دشپات) را تعیین می کند. این رابطه در "مقدمه ای بر چسب ها" توسط شرکت Three Bond، ژاپن ساده شده است.
شکل 13 : مفهوم ویسکوالاستیک
نوع اول که در این مطالعه با عنوان " نوع A" از آن یاد می شود، از نوع ماستیک با مقاومت برشی بالا است. این نوع HSS به طور گسترده در کاربردهایی استفاده می شود که در آن قرار گرفتن در معرض تنش مکانیکی متوسط مورد انتظار است.
نوع دوم که در این مطالعه به عنوان " نوع B" نامیده می شود، دارای ماستیک نوع سنتی با مقاومت متوسط تر است که حاوی درصد قابل توجهی لاستیک بوتیل با آسفالت، عوامل فعال کننده و رزین های چسبنده است. این HSS به طور گسترده در کاربردهایی استفاده می شود که در آن با یک لایه "پرکننده" پوشانده شده است، که معمولاً از فوم پلی اورتان یا الاستومر جامد پلی اورتان تشکیل شده است، مانند روش طراحی معمول برای خطوط لوله با پوشش بتنی.
4.4. مدل های جدایش سطحی و منسجم
هنگام آزمایش عملکرد چسب ها، چه با روش لایه برداری یا برش لبه، نتیجه ثبت شده معمولاً به عنوان معیاری از مقاومت برشی / لایه برداری و حالت جدایش ارائه می شود. حالت ها یا جدایش منسجم ، یا جدایش سطحی می باشد. در شرایطی که خوردگی بستر فولادی یک نگرانی است، حالت جدایش منسجم به طور معمول مشخص می شود، یعنی اطمینان از اینکه قدرت پیوند میانی بالاتر از قدرت خود چسب است، و از باقی ماندن لایه ای از مواد محافظ چسب بر روی بستر فلزی اطمینان حاصل می شود.
در این تحقیق، ارزیابی عملکرد بر پایه ارزیابی تغییر در حالت جدایش است. همان طور که در 4.1 نشان داده شده است و در ضمیمه C توضیح داده شده است، "شروع" یا "آستانه" جدایش چسب را می توان با افزایش سرعت لایه برداری ارتقا داد. از این رو حفظ سرعت لایه برداری ثابت اهمیت دارد.
5.4. چسبندگی و خوردگی
خزش خوردگی در زیر پوشش به دلیل تشکیل، انبساط و انتشار محصولات خوردگی در زیر پوشش و روی سطح زیرلایه صورت می گیرد. تقریباً (به شماتیک مراجعه کنید) مانند یک "اهرم" که از پوشش جدا می شود، همان طور که در شکل 16 نشان داده شده است .
شکل 16: تاول اسمزی به دلیل وجود نمک های محلول در سطح مشترک فلز / رنگ.
چسبهای با استحکام بالا، مانند اپوکسیها، نه تنها استحکام ساختاری بسیار بالایی دارند، مانند آنچه در صنعت خودروسازی و هوافضا استفاده میشود، بلکه میتوانند عملکرد ضد خوردگی عالی را نیز ارائه دهند. آن ها دارای خواص مرطوب کنندگی عالی هستند، سطحی بالایی از اتصال را ایجاد می کنند و پس از پخت، استحکام پیوند بسیار بالایی ایجاد می کنند. این امر تشکیل تاول و یا از هم گسیختگی پوشش را کاهش می دهد. به طور خلاصه می توان گفت که اپوکسی ها می توانند استحکام چسبندگی و چسبندگی بسیار بالایی داشته باشند اما نیاز به آماده سازی سطح بسیار خوبی دارند.
در مقایسه با چسبهای با استحکام بالا، ماستیکها را میتوان بیشتر به عنوان درزگیر در نظر گرفت تا چسب، زیرا با «آب بندی» بستر از آب، مانع از توسعه محصولات خوردگی میشوند. ماستیک ها همچنین به "خیساندن" خوب زیرلایه متکی هستند و از نفوذ آب و اکسیژن جلوگیری می کنند. با این حال، آن ها چسبناک هستند و ویژگی "لزج" خود را حفظ می کنند. آن ها با ادامه ایجاد چسبندگی سطحی، از خوردگی جلوگیری می کنند. ماستیک های خوب همچنین دارای خواص بازدارندگی عالی هستند و از نفوذ رطوبت به بستر جلوگیری می کنند. ماستیک هایی که به راحتی در دمای عملیاتی خود جریان می یابند و توانایی جریان یافتن به نواحی آسیب دیده مانند خراش ها و حفره های کوچک را دارند "خود ترمیم شونده" هستند و در صنعت پوشش خطوط لوله به "ویسکو الاستیک" معروف شده اند.
خواص زیر سازی عامل مهمی در سرعت خوردگی زیر پوشش است. منطقی است که برای یک پوشش بدون منفذ (یعنی بدون وقفه در یکپارچگی پوشش)، درجه خوردگی متناسب با نفوذ اکسیژن و رطوبت از پوشش باشد. بنابراین، نفوذپذیری پوشش به اکسیژن و رطوبت و همچنین ضخامت پوشش تأثیر قابل توجهی بر سرعت انتشار خوردگی زیرلایه فولادی و در نتیجه از هم گسیختگی پوشش دارد. 2LHSS نسبتاً ضخیم هستند (معمولاً حدود 2 میلی متر)، با خواص پوششی خوب، و دارای چسب های ویسکوالاستیک بالا هستند.
عامل دیگری که باید در نظر گرفته شود این است که "نیروهای اسمزی" از تفاوت در غلظت محلول در دو طرف غشا ایجاد می شوند. این بر اساس وجود محلول نمک بیشتری در زیر فیلم به دلیل نمک های به دام افتاده می باشد. در مورد پوششهای غوطهور در آب شور، به دلیل اختلاف شوری کاهش یافته، فشار اسمزی در بستر آلوده به نمک، احتمالاً شدیدتر است.
ماستیکها عموماً دارای استحکام چسبندگی پایین و متوسطی هستند و اگرچه آمادهسازی خوب سطح اهمیت دارد ، اما وجود محصولات خوردگی و نمکهای موجود ممکن است برای این نوع پوشش حیاتی نباشد.
6.4. خزش / ازدیاد طول لایه پشتی HDPE روکش انقباض حرارتی
در طی تولید HSS، لایه پشتی پلی اتیلن با چگالی بالا (توجه داشته باشید: برخی از HSS ها دارای لایه پشتی پلی پروپیلن هستند) به صورت پیوندهای پیچیده متصل می شود. پوشش گرم می شود و در جهت طولی کشیده می شود و در حالی که کشیده می شود خنک می شود. پیوند پیچیده منجر به درجه بالای خاصیت ارتجاعی می شود. هنگامی که پوشش در حالت پلاستیکی خود کشیده می شود و سپس سرد می شود، بر اثر تنش در آن قفل می شود. گرم کردن مجدد HSS باعث انقباض آن به اندازه اولیه (بدون تنش) می شود. بیشتر کشش در جهت طولی HSS ( در جهت شعاعی لوله) رخ می دهد. پس از اینکه HSS به اندازه قطر لوله کوچک شد، "تنش حلقه" باقی مانده همچنان HSS را مانند یک نوار الاستیک به لوله می کشد.
فرض بر این است که در طی پیرسازی توسط آب داغ، این تنش حلقهای، نیروهای فشاری در HSS ایجاد میکند و از آن جایی که حلقههای لوله کوتاه جلوی امتداد طولی را نمیگیرد، HSS تمایل به خزش یا انبساط طولی دارد. لایه اپوکسی توصیه شده توسط تامین کننده که بر روی انتهای لوله صاف (بدون سنگ ریزه) اعمال می شود، به راحتی با انبساط HSS جابجا می شود و ظاهراً از سطح "ترک خورده" دور می شود. تغییر به یک پوشش انعطاف پذیرتر (یا ماستیک) مانند یک محصول بر پایه سیلیکون ممکن است برای ارزیابی های آینده ارزش توجه داشته باشد.
5. نتیجه گیری
بررسی مقاله نشان داد که اطلاعات منتشر شده کمی در مورد آزمایش 2LHSS وجود دارد و در این نوع پوشش، چسبندگی هیچ ارتباطی به آزمایش غوطه وری در آب گرم ندارد. از این رو، نتایج این بررسی، دادههای صنعتی مفیدی را در رابطه با اثر پیرسازی توسط آب گرم و تأثیر آلودگی نمک سطحی بر قابلیتهای پیش گیری از خوردگی مناطق سرجوش ارائه کرده است.
مقدار بالای نمک دریا بر روی سطوح لوله های آماده سازی شده با ابزار برقی با آزمایش لایه برداری 2LHSS پس از غوطه وری در آب داغ مورد بررسی قرار گرفت و با آزمایش های لایه برداری انجام شده قبل از غوطه وری در آب داغ مقایسه شد.
شرایط آزمون شدید در نظر گرفته شد: سطوح آلوده نمکی تا 120 میلی گرم در متر مربع روی سطوح لوله تمیز شده با ابزار برقی که به مدت یک سال بدون سنگ ریزه قبلی پیرسازی شده اند اعمال می شود. روند پیری تسریع شده دو برابر مدت زمان غوطه وری تعیین شده در آب داشت و نمونه های آزمایشی دارای لبه های آشکار بودند که امکان جا به جایی رطوبت را در زیر پوشش فراهم می کرد.
نتایج آزمایش نشان داد که هیچ اثر مضر قابل توجهی بر عملکرد دو پوشش سر جوش میدانی که معمولاً 2LHSS مورد استفاده قرار می گیرد، وجود ندارد. بنابراین، به این نتیجه رسیدیم که با توجه به اینکه میزان آلودگی نمک روی سطوح لوله های آماده شده پس از آزمایش غیر مخرب مرطوب، معمولاً بسیار کمتر از سطوح آزمایش شده در این مطالعه است، سطوح لوله های آماده شده برای استفاده از نوع 2 لایه HSS نیازی به ویژگی خاصی ندارند. اقدامات برای کاهش بیشتر آلودگی نمک اضافی است، مشروط بر اینکه مراقب باشید که این شرایط به طور مداوم در طی عملیات لوله گذاری حفظ شود.
6. توصیه ها و مطالعات بیشتر
یافتههای حاصل از این مطالعه اولیه نشان میدهد که سطوح آلودگی نمک محلول تا حدود 120 میلیگرم بر متر مربع باید توسط دو مورد از متداولترین نوع روکش های انقباض حرارتی دولایهای که برای پوشش سرجوش میدانی خط لوله استفاده میشوند قابل تحمل باشد. این نتیجه گیری بر اساس نتایج قابل قبول به دنبال روش آزمایشی است که معمولاً برای تشخیص نمک های محلول (یعنی آزمایش غوطه وری در آب داغ) استفاده می شود.
برای بهبود اطمینان، بر اساس روشها، یافتهها و نتایج این مطالعه، آزمون جدایش کاتدی باید با استفاده از بالاترین غلظت آلودگی نمک باقیمانده در نظر گرفته شود تا اطمینان حاصل شود که چسبندگی پوشش قابل قبول و عملکرد جلوگیری از خوردگی حتی در شرایط حفاظت کاتدی بیش از حد حفظ میشود.
اگر چه اثر آلودگی نمک تایید شده است، دلایل کلیدی برای بی اهمیت بودن آن بر HSS پشت ماستیک 2HSS به طور کامل مشخص نشده است. تحقیقات بیشتر در مورد تأثیر نسبی سطوح بالای آلودگی نمک محلول بر روی 3LHSS در مقایسه با 2LHSS، با استفاده از چسب HSS یکسان و لایه پشتی HSS یکسان، تأیید می کند که آیا مکانیسم شکست متفاوت یک اپوکسی در مقایسه با ماستیک عامل حیاتی در تاثیر عملکرد میدانی است یا خیر. از سوی دیگر، می توان نتیجه گرفت که ماستیک ضخیم و لایه پشتی پلی اولفین مانعی برای نفوذ رطوبت ایجاد می کند که از جدا شدن روکش مناطق سرجوش از ناحیه جوش خورده جلوگیری می کند.
حتی اگر مطالعه بیشتر برای تعیین اینکه ماستیک و لایه پشتی پلی اولفین HSS مانع مؤثرتری برای نفوذ رطوبت است، از دیدگاه طراحی، سناریوی شکستگی در یکپارچگی پوشش (یعنی منافذ) باید در نظر گرفته شود. یافتههای این تحقیق تأیید کرد که هیچ جا به جایی قابلتوجهی از رطوبت در زیر ماستیک در انتهای لوله در معرض سیستم 2LHSS رخ نداده است.
همچنین لازم به ذکر است که به طور کلی در نظر گرفته می شود که پرایمرهای اپوکسی عملکرد ضد خوردگی عالی بر روی سطوح به خوبی آماده شده دارند و عملکرد بسیار بهتری نسبت به ماستیک ارائه می دهند. اما نتایج آزمون حاضر این نظریه را تأیید نکرد. بنابراین، از آن جایی که اهداف استفاده از پرایمرهای اپوکسی بالاتر است، اگر بخواهیم 3LHSS بر پایه بر اپوکسی را مشخص کنیم، باید از روشهای آزمون دقیقتری استفاده شود.