این مقاله شامل داده های کلیدی خط لوله انتقال MONACO در Upper Bavaria آلمان است. ساخت جدید خط گاز طبیعی فشار قوی نقطه عطف مهمی برای تامین امنیت در منطقه است.
پوشش سرجوش میدانی - چالش واقعی
مانند هر محل ساخت و ساز دیگری، چالش های خط لوله MONACO بسیار خاص و منحصر به فرد است. بر خلاف پوشش های کارخانه ای، که در آن لولههای فولادی تحت شرایط تولید ایدهآل با یک سیستم محافظ پوشش داده میشوند، در هنگام پوشش دهی مناطق سرجوش در پروژه، گاهی اوقات عوامل خارجی بسیار دشوار باید در خود محل پروژه در نظر گرفته شوند. عوامل مهم در حین نصب شامل ویژگی های خاص آب و هوا، خاک و زمین مربوطه می باشد. در مقابل، برای بهره برداری از خط لوله، حفاظت در برابر منابع خورنده و مقاومت خط لوله در برابر تنش های مکانیکی مانند حمل و نقل و حرکت لوله اهمیت ویژه ای دارد.
پوشش سرجوش میدانی شامل چالشهای متعددی است: علاوه بر فرایند آسان و ایمن، یکی از مهمترین معیارهای تصمیمگیری پوشش سرجوش، مقاومت ثابت شده دراز مدت در برابر پیری در طی دههها کارکرد است. زیرا به عنوان اولین خط دفاعی، جلوگیری از خوردگی غیرفعال (پسیو) مانع از رسیدن محیط خورنده به سطح فولاد می شود. باید با مقاومت های قابل اثبات از نظر مقاومت لایه لایه شدن و استحکام کششی و همچنین مقاومت در برابر فرورفتگی، ضربه و پارگی با معیار های پذیرش مطابقت داشته باشد (شکل 1). جریان حفاظت کاتدی تنها به عنوان "خط دوم دفاعی" در صورت عدم اختلال در جلوگیری از خوردگی غیرفعال مداخله می کند.
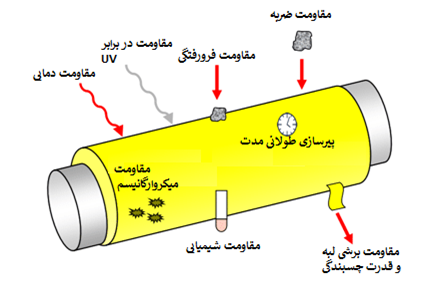
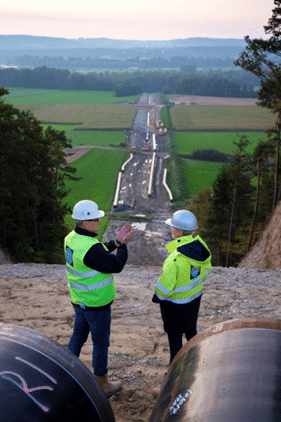
شکل 2: شیب تند MONACO، آلمان
در امتداد بخش ساختمانی ظاهراً کوتاه خط لوله MONACO، که تقریبی اندازه گیری شده، انواع زمین های مختلف وجود دارد. 40 کیلومتر، پروژه بسیار بزرگی را می طلبد. تعدادی از رودخانهها، خطوط قطار، گذرگاهها ( به عنوان یک چالش خاص ) در یک مسیر با شیب تند (شیب 50 درصد) باید فتح شود. افراد، مواد و ماشین آلات باید بتوانند هنگام جوشکاری لوله ها و متعاقباً عایق کاری درزهای جوش در این شیب، الزامات بسیار دقیق را برآورده سازند.
تکنولوژی سه لایه برای محافظت از لوله
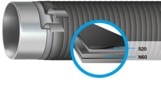
برای این بخش ساخت و ساز، از سیستم دو نواری استفاده شده است که خود را در طی دهه ها ثابت کرده است. سیستم اعمال سرد برای جلوگیری از خوردگی در لوله های فلزی از دو نوار سه لایه اکسترود شده تشکیل شده است که به عنوان یک لایه نوار داخلی و خارجی روی خطوط لوله اعمال می شود (شکل 3).
ساختار این نوارهای سه لایه خود ادغام شونده از یک لایه حامل از جنس پلی اتیلن تشکیل شده است که از دو طرف با یک لایه چسب از جنس لاستیک-بوتیل پوشانده شده است. این لایه حامل در یک فرآیند هم اکستروژن خاص ساخته می شود که در آن یک واحد جدا ناپذیر از مواد حامل و مواد پوشش ایجاد می شود. در نتیجه، فیلم نمی تواند از لایه های چسب خود جدا شود، همان طور که گاهی اوقات در مورد نوارهای چند لایه دیده می شود.
یک پوشش مارپیچی شکل با همپوشانی 50 درصدی نوارهای سه لایه در اطراف لوله به لایه های چسب بوتیل اجازه می دهد تا در نواحی همپوشانی با هم ترکیب شوند. آن ها یک پوشش همگن را تشکیل می دهند و به طور جدایی ناپذیر به یکدیگر متصل می شوند. در این نواحی، مولکول های لایه های لاستیک-بوتیل با هم ترکیب می شوند. این فرآیند خود آمیختگی تنها پس از مدت کوتاهی - حداکثر پنج روز - تکمیل می شود (شکل 4 تا 7).
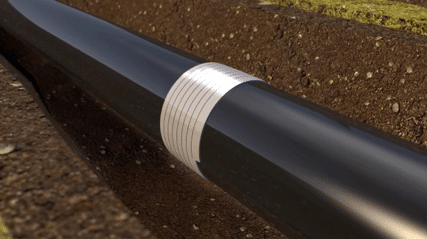
شکل 4: نوار پیچی با 50% همپوشانی
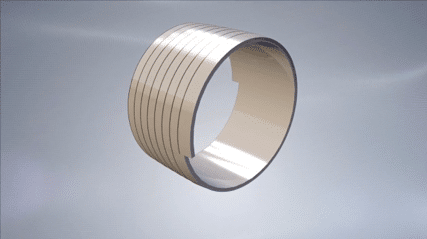
شکل 5: نوارهای خود ممزوج

شکل 6: حفاظت دائمی لوله
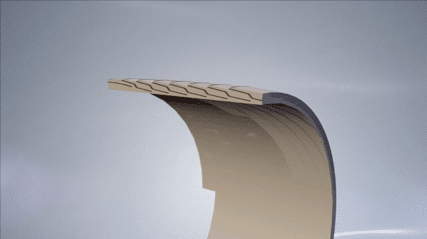
شکل 7: پیشگیری از خوردگی مورد تأیید
در مقابل، نوارهای دو لایه اثر خود ممزوج شدگی ندارند. به عبارتی دیگر، فیلم حامل پلی اتیلن فقط در یک طرف دارای یک پوشش چسبنده است. هنگامی که از نوارهای دو لایه استفاده می شود، در صورت فرسودگی چسب و در نتیجه ورود اکسیژن و رطوبت، فرآیندی به نام لایه لایه شدن رخ می دهد، به این معنی که لایه محافظ در برابر خوردگی از سطح فولاد جدا می شود. هنگامی که همپوشانی های نواری به طور ناقص انجام شود، استفاده از نوارهای دو لایه نیز باعث آسیب شدید مانند خوردگی مارپیچی می شود.
فناوری نوار سه لایه در مقایسه با سایر روش های پیشگیری از خوردگی (مانند پوشش های قابل انقباض حرارتی، پوشش های مایع و غیره) مزایای بسیاری دارد. این نوارهای جلوگیری از خوردگی، نیاز کاربر و اپراتور را برای فرایند ساده، قابل اعتماد و کارآمد به خوبی برآورده می کند. این نوارها به روش سرد اعمال می شوند. ابزار اضافی مانند مشعل برای ذوب یا پیش گرم کردن لوله فولادی لازم نیست. لوله فقط نیاز به فرچه کشیدن دارد و نیازی به سند بلاست ندارد. بنابراین، نوار را می توان در زمانی که خط لوله در حال استفاده است نیز اعمال کرد(یک مزیت قابل توجه در هزینه برای اپراتور). استفاده از نوارهای محافظ در برابر خوردگی آنقدر گسترده است که می توان از نوارها در قطرهای اسمی مختلف در یک محل پروژه استفاده کرد. پیش مونتاژ هماهنگ با قطر لوله در محل کار ضروری نیست. نوارپیچی اضافی نیز می تواند به سرعت و به راحتی برای اصلاح هر گونه نقص یا خطا در فرایند اعمال شود. تکنولوژی نوار سه لایه: یک راه حل با مزایای بسیار است.
پیتر وستفال، این موضوع را به صورت زیر خلاصه میکند: « مزیت سیستم دو نواری به سادگی این است که یک نوار سه لایه است که در دو لایه روی لوله اعمال میشود. با گذشت زمان، نوارها با هم ترکیب میشوند و مانع از خوردگی طولانی مدت میشوند.» سیستم نواری با کارایی بالا که در خط لوله MONACO استفاده می شود، سیستمی است که طبق استاندارد پیشرو EN 12068، کلاس تنش C50 آزمایش شده و توسط انجمن فنی و علمی آلمان برای گاز و آب (DVGW) مورد تایید قرار گرفته است. برای دماهای تا 70+ درجه سانتی گراد (158+ درجه فارنهایت) مناسب است و با تمام پوشش های کارخانه ای ساخته شده از PE، PP، FBE، P، CTE و قیر سازگار است.
پیشگیری از خوردگی اثبات شده پس از چهار دهه
به ویژه در ساخت خط لوله با چرخه های عملیاتی بسیار طولانی، تأیید عملی یک راه ایده آل برای اثبات این نظریه است. فرصتی برای چنین تاییدی در سال 2015 در آلمان به وجود آمد. یک مرکز لجستیک مدرن برای یک خودروساز دقیقاً در همان منطقه ای ساخته شد که خط گاز طبیعی فشار قوی ISARSCHIENE برای اولین بار در سال 1976 بین Moosburg و Straubing در Bavaria ساخته شد. به عنوان بخشی از مسیریابی مجدد خط گاز که به ساخت و ساز جدید نیاز داشت، لوله های 39 ساله توسط اپراتور حفاری شدند.
این یک فرصت منحصر به فرد برای بررسی دوام و کیفیت نوار بود که در طی ساخت اولیه استفاده شده بود. با پیشرفت آزمونهای کنترل کیفیت، تمام محصولات تحت طیف وسیعی از آزمایشهای کیفی قرار میگیرند که ویژگیهای پیرسازی طولانی مدت مواد را شبیهسازی میکند. تجزیه و تحلیل یک نوار از یک خط که در واقع به مدت 39 سال مورد استفاده مداوم قرار گرفته بود، نتایج بسیار جالب و دقیقی را نشان داد.
اولین شگفتی برای تیم متخصص در حین کار حفاری رخ داد: لوله از یک تن خاک بازیابی شد. تکنولوژی پیشرفته کنونی مستلزم قرار دادن لوله بر روی یک بستر شنی است. با این وجود، در مناطقی که توسط نوار محافظت می شد، لوله هیچ نشانه ای از آسیب خوردگی نشان نمی داد. لایه لاستیک بوتیل به طور ایمن روی فولاد چسبانده شده و حفاظت کاملی را برای لوله فراهم می کند (شکل 8).
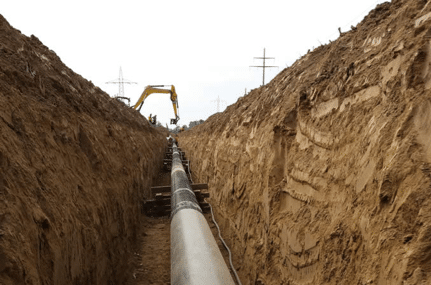
شکل 8: حفاری Isarschiene، آلمان
آنالیز آزمایشگاهی شماره درز جوش حفاری شده 584 با قطر لوله DN 300 به ویژه آشکار بود. اگرچه این خط لوله در منطقه تولید غلات آلمان واقع شده است، جایی که به دلیل تراکتورهای سنگین و ماشین آلات برداشت، ارتعاشات زمین انتظار می رود، پوشش خط لوله در فشار بالا حتی پس از چهار دهه استفاده، هیچ نقصی نشان نداد. کل منطقه درز جوش داده شده لوله فولادی هنوز به طور کامل توسط نوار سه لایه در برابر خوردگی محافظت می شد.
در سال 1976، نوار با مشخصات استاندارد برای استحکام لایه برداری 8 نیوتن بر سانتی متر مطابق با DIN 30672 اعمال می شد. آزمایش در استاندارد فعلی مطابق با EN 12068 به استحکام لایه برداری بالاتر 10 نیوتن بر سانتی متر نیاز دارد. پس از 39 سال، اندازهگیریها یک الگوی جداسازی منسجم با قدرت لایهبرداری خارقالعاده. N/cm 18.3 را نشان داد. بنابراین نتایج آنالیز 83 درصد از الزامات امروزی فراتر می باشد (شکل 9).
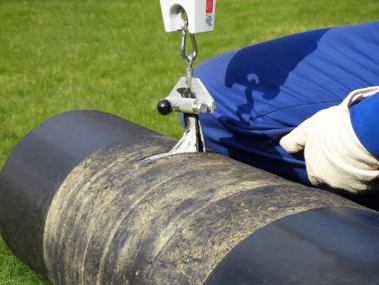
شکل 9: الگوی جداسازی منسجم پس از 39 سال
زمین های ناهموار به دستگاه های نوارپیچ تخصصی نیاز دارند
بازگشت به خط لوله MONACO: تمرکز مشتری در اجرای نوار پیچی، بر اتوماسیون و کارایی است. تجهیزات نوار پیچی با سوخت بنزینی یا الکتریکی، سطح بالایی از قابلیت اطمینان استفاده را تضمین میکنند و به طور خودکار کشش و عرض همپوشانی ثابت را در نوار پیچی حفظ میکنند . با استفاده از این تجهیزات، حجم کار کارکنان به میزان قابل توجهی کاهش می یابد. ماشینهای نوار پیچی در مقایسه با نوار پیچی دستی 50 درصد سریعتر و در نتیجه کارآمد تر می باشد.
برای این پروژه سخت با شیب های تند، گذرگاه های قطار و رودخانه و همچنین گذرگاه های جاده، می توان از دستگاه نوار پیچی های سبک و کوچکتر به طرق مختلف استفاده کرد. به دلیل سبک بودن، این قبیل دستگاه ها برای استفاده در زمین های صعب العبور، مانند شیب تند و همچنین برای پوشش مناطق زانویی لوله های کوتاه و برای عرض های اسمی کوتاه DN 40، ایده آل است.
در تابستان 2018، پس از پایین آوردن خط لوله و پر شدن سیال ، آزمایشهای فشار آب برای بررسی نفوذناپذیری درزهای جوش انجام شد. آزمایش پوشش سرجوش میدانی ، نتایج کاملی را نشان داد. کار ساخت و ساز در سال 2018 تکمیل شد و خط لوله در آوریل 2019 به بهره برداری رسید.