خوردگی می تواند منجر به عواقب غیر قابل پیش بینی شود. استفاده مداوم از اقدامات حفاظتی در برابر خوردگی می تواند خطر را به میزان قابل توجهی کاهش دهد. نه تنها توسعه پوشش ها برای بهبود حفاظت در برابر خوردگی مورد نیاز است، بلکه اجرای درست پوشش در شرایط محلی پروژه و حساسیت نصب از اهمیت بالایی برخوردار است. سیستم حفاظت از خوردگی در یک شبکه لوله باید از جنبه های مختلف کاربری بررسی شود. سازگاری سیستم های مختلف با یکدیگر و تشخیص ضعیف ترین حلقه در زنجیره، پیش نیازهای یک سیستم شبکه حفاظت از خوردگی طولانی مدت است.
سیستم های حفاظت از خوردگی غیرفعال طبق استاندارد DIN 30672 تایید شده اند. علاوه بر این، DVGW مطابق با کاربرگ GW 15 به آزمایش نصب کننده نیاز دارد، اما DIN نمیتواند حساسیت استفاده از یک سیستم حفاظت در برابر خوردگی غیرفعال را پوشش دهد و نتایج آزمایش نشان می دهد که نقاط بحرانی یک برنامه کاربردی را در شرایط میدانی در نظر میگیرد.
حفاظت از خوردگی غیر فعال
به غیر از حفاظت در برابر خوردگی به روش حفاظت کاتدی، روش دیگری که استفاده می شود، استفاده از سیستم حفاظت در برابر خوردگی غیرفعال است. "غیرفعال" در این زمینه به این معنی است که سیستم حفاظت در برابر خوردگی با فرآیند خوردگی الکتروشیمیایی تداخلی ندارد. پوشش محافظ دور جسم پیچیده می شود و از آن در برابر محیط خورنده محافظت می کند.
سیستم های حفاظت از خوردگی غیرفعال، به دو نوع پوشش های کاربردی کارخانه و میدانی تقسیم بندی می شوند.
پوشش های مورد استفاده کارخانه ای
پوشش های کارخانه ای توسط تولید کنندگان لوله یا اتصالات لوله اعمال می شود. این ها پوشش های دو لایه یا سه لایه هستند (شکل 1). تصویر 1a یک پوشش سه لایه را نشان می دهد که قبل از اعمال پلی اتیلن لایه ای از پوشش رزین اپوکسی استفاده می شود. اما یک پوشش دو لایه بدون اپوکسی اعمال می شود. هر دو سیستم دو لایه و سه لایه شامل یک لایه چسب نیز هستند که برای ایجاد اتصال به لایه پلی اتیلن ضروری است.
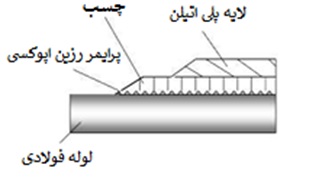
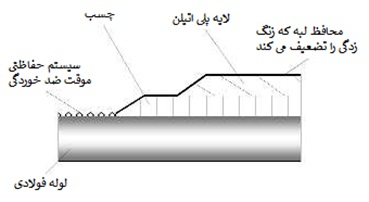
شکل 1: a) پوشش کارخانه ای 3 لایه b) پوشش کارخانه ای 2 لایه
پوشش های کاربردی میدانی
پوشش های میدانی موادی هستند که در محل پروژه اجرا می شوند. الزامات پوشش های اعمال شده در پروژه در استاندارد DIN 30672 بخش 1 تعیین شده است که در سال 1972 صادر شد.
با بهبود پوشش های اعمال شده در کارخانه، الزامات برای پوشش های اعمال شده در میدان افزایش می یابد. استاندارد DIN در سپتامبر 1991 بازنگری و دوباره صادر شد.
با این حال، استاندارد DIN 30672 فقط به نوارهای ترموپلاستیک، قیر و محصولات انقباضی محدود می شود و شامل مواد واکنش دوروپلاستیک نمی شود. (مواد دوروپلاستیک ساخته شده از رزین های پلی استر غیر اشباع یا وینیل استر هستند، که با الیاف شیشه و کربن تقویت شده اند.) الزامات این موارد را می توان در DIN 30672، بخش 2 مشاهده کرد.
الزامات برای پوشش های اعمال شده در پروژه در استاندارد DIN 30672 آمده است. این موضوع به طبقه بندی تنش و دما تقسیم می شود که از آن ماتریکس زیر مشتق شده است.
A-B-C طبقه بندی تنش برای خواص مکانیکی پوشش های اعمال شده در پروژه هستند. C بالاترین کلاس است. طبقه بندی دما به دو حالت تقسیم می شود.
کاربرگ DVGW GW 15
به غیر از استاندارد DIN 30672، مجموعه قوانین DVGW (انجمن آلمان در بخش گاز و آب) برای صدور گواهی نامه اجرا کننده های پوشش در پروژه (مجریان) وجود دارد که در آلمان از اهمیت زیادی برخوردار است.
"پوشش خطوط لوله با مواد آلی پوشش دهی با کیفیت بالا در کارخانه ، با دانش تخصصی مجریان در هنگام اعمال پوشش های در محل پروژه بایستی تکمیل شود. پوشش های مورد استفاده با کیفیت بالا در دسترس هستند که طبق الزامات DIN 30672 استاندارد شده اند. استفاده از این پوشش ها مستلزم صلاحیت در نصب و همچنین دانش صحیح در مورد خود مواد هستند. "
اعضای DVGW کمیته تخصصی "حفاظت در برابر خوردگی بیرونی" مسئول پوشش های اعمال شده در پروژه هستند و در ایجاد استاندارد DIN 30672 نقش اساسی داشتند.
کاربرگ DVGW برنامههای آموزشی و آزمایشی را برای نصب پوششهای مورد استفاده در پروژه بر روی لولهها، اتصالات و سرپیچ ها ارائه میکند. این کاربرگ شامل یک برنامه آموزشی عملی به همراه یک آزمون جامع برای اجرا کنندگان می باشد. در پایان برنامه آموزشی، آزمونی برای تعیین میزان دانشی که در طی دوره آموزشی کسب کرده اند، وجود دارد. این آزمون با ارائه پاسخ به سوالات کتبی انجام می شود. مدت زمان آموزش و آزمون 16 ساعت می باشد. در صورتی که اجرا کننده آزمون را قبول شود، یک "گواهی نامه اجرا کننده" به او داده می شود، که به مدت سه سال اعتبار دارد و عملاً در اجرای تمام پوشش های اعمال شده در محل های پروژه در آلمان مورد نیاز است.
سیستم های پوشش مورد استفاده در پروژه
سیستم های پوشش دهی به دو دسته سیستم های سرد و گرم تقسیم می شوند. تعریف سیستم نواری گرم اعمال شده این است که انرژی (حرارت) معمولاً با استفاده از یک مشعل گاز مایع به پوشش انتقال می شود. هنگامی که از نوارهای قیری استفاده می شود، مشعل لازم است تا قیر را روی سطح نوار ذوب کند و نوار در حالت پلاستیکی خود نوعی چسبندگی به سطح لوله داشته باشد.
مواد انقباضی متشکل از پلی اتیلن با ترکیب پیچیده تحت تابش قرار گرفته، با شرایط تنش محبوس، پوشش داده شده با چسب می باشد. هنگامی که حرارت اعمال می شود، پلی اتیلن نرم می شود. به دلیل تنش داخلی این نوع مواد ، پلی اتیلن شروع به انقباض می کند و لوله ای را که روی آن قرار گرفته است محکم می پوشاند.
در واقع در این روش، هیچ پرایمری مورد نیاز نیست، زیرا این پوشش به طور یکپارچه با ماده ای مجهز شده است که نه تنها از سطح محافظت می کند، بلکه به آن کاملا می چسبد. لایه پشتی قابل انقباض، حفاظت مکانیکی را فراهم می کند و نیرو را به طور مساوی در اطراف لوله توزیع می کند. با توجه به مقاومت در برابر نفوذ برتر و نیروی انقباض بالا، جنس لایه پشتی باید از پلی اتیلن با چگالی بالا باشد.
سیستم های کاربردی سرد نیازی به گرما ندارند. فقط آماده سازی سطح لوله، یعنی خشک کردن و پیش گرم کردن، باید با استفاده از مشعل گاز مایع انجام شود.
نوارهای پترولاتوم (نوارهای وازلین) از مواد پشت بند آغشته به پترولاتوم پایدار الاستیک (ترکیب اشباع شده از کربوهیدرات ها) تشکیل شده و از یک طرف با نوار پلی اتیلن پوشانده شده است.
نوارهای مصنوعی (پلاستیکی) از یک ماده لاستیک بوتیل تشکیل شده است که با توجه به نوع آن، می توان آن را با نوار پلی اتیلن پوشاند. لاستیک بوتیل در واقع وظیفه محافظت در برابر خوردگی را بر عهده دارد و روی پرایمری که قبلا استفاده شده و از قبل خشک شده است (در هر مورد طبق دستورالعمل سازنده، با 50 درصد همپوشانی هنگام پیچاندن دور لوله) اعمال می شود. برای حفاظت مکانیکی بیشتر، اولین لایه لاستیک بوتیل با لایه دوم نوار پلی اتیلن پوشانده شده است.
حفاظت در برابر خوردگی با استفاده ویژه از چسب
محصول جانبی، محافظت در برابر خوردگی، همان طور که گفته شد، از پیوند سرجوش ها به دست میآید و برگرفته از این واقعیت است که چسبها و پلیمرها مواد رسانا نیستند. وجود لایه چسب بین دو قطعه فلزی متصل شده، از تشکیل خوردگی گالوانیکی جلوگیری می کند و چسب به عنوان یک لایه محکم از دسترسی به محیط های خورنده جلوگیری می کند.
چسب ها فقط زمانی امکان حفاظت از خوردگی غیر فعال موثر را فراهم می کنند که بتوانند به چسبندگی طولانی مدت کافی دست پیدا کنند. فقط در این شرایط چسب ها می توانند از تماس مواد خورنده با سطح (فولاد) جلوگیری کنند. پیوند به دلیل برهم کنش شیمیایی و فیزیکی بین مولکول های چسب و بستر تشکیل می شود. درستی تشکیل پیوند مواد به سطوح، موضوع تحقیق فعلی است و هنوز به اندازه کافی روشن نشده است. با این حال، آزمایشهایی که مکانیسم اتصال چسبها به سطوح فلزی را توضیح میدهند، پیوند پیچیدهای را بین چسبهای رزین اپوکسی و فولاد ایجاد میکنند.
این مکانیسم پیوند بر اساس اتصالات چرخه ای (کی لیت ها) می باشد؛ که ثابت شده است بسیار مقاوم در برابر رطوبت هستند. از نظر فنی، این کشف در زمینه حفاظت از خوردگی غیرفعال با استفاده از پرایمرهای بر پایه اپوکسی و چسبهای رزین اپوکسی که در لایههای ضخیم کافی اعمال میشوند، استفاده میشود.
حفاظت در برابر خوردگی غیرفعال به هیچ خاصیت مرتبط با استحکام چسب نیاز ندارد. این وضعیت اجازه می دهد تا (PSA ) چسب حساس به فشار در پوشش های اعمال شده در پروژه استفاده شود. PSA نشان دهنده یک گروه چسب ویژه می باشد که سفت نمی شود. آن ها به عنوان مایعات چسبناک دائمی دیده می شوند و بسیار چسبناک هستند و به طور گسترده در تجارت و صنعت استفاده می شود. کاربرد آن ها از رنگ کاری، نوارهای عایق گرفته تا کاربردهای سخت در هواپیماها را شامل می شود.
وجه مشترک همه چسب های PSA حساسیت فشار آن است. استحکام قابل دستیابی یک پیوند (یعنی میزان نیروی چسبندگی با چسبندگی کافی) به فشار پانتوگراف[ابزاری برای کپی کردن یک نقشه یا پلان در مقیاسی متفاوت توسط سیستمی از میله های لولایی و اتصالی] بستگی دارد.
با استفاده از یک ویژگی پایداری در چسبندگی، عملکرد و انسجام چسب را می توان به طور گسترده تغییر داد. بر اساس فرمول و فرایند چسب های ساختمانی، رفتار جریان، کم و بیش وابسته به دما می باشد. این با مقدار رزین و ساختار پلیمر تعیین می شود. برای اینکه بتوان از آن ها برای پوشش های کاربردی در پروژه استفاده کرد، باید معیارهای زیر رعایت شود:
· چسبندگی خوب
· رفتار جریان خوب، حتی در دماهای پایین (رطوبت بهینه سطح)
· پایداری کافی برای دمای مورد نیاز
برای این که بتوان به چسبندگی خوبی دست یافت، چسب، صرف نظر از نوع آن، باید سطح جامد را خیس کند. در این حالت خیس شدن به معنای نزدیکی مایع به سطح در مقیاس اتمی است. مولکول های چسب بایستی در محدوده پیوند به سطح نزدیک شوند که در پیوند کووالانسی اولیه (پیوند یگانه) و ثانویه (پیوند چندگانه) به یک مقدار 0.1 تا 0.5 نانومتر می رسد. اگر مواد دیگری روی سطح باشند، هیچ چسبندگی به ماده واقعی حاصل نمی شود، بلکه فقط این چسب به لایه های ناشناخته می تواند برسد. این ثابت می کند که، اگر میخواهید چسبندگی بهینه برای محافظت طولانیمدت در برابر خوردگی حاصل شود، هر لایه ای که مانع خیس شدن سطح شود، به عنوان مثال گریس، گرد و غبار یا اکسید ها باید حذف شوند.
کاربرد و آماده سازی لوله پوشش های میدانی
پوششهای میدانی فعلی ( DIN تأیید شده) در صورتی که طبق دستورالعملهای رسمی نصب اعمال شوند، محافظت بسیار خوبی در برابر خوردگی ایجاد میکنند.
با این حال به ویژه در مورد پوشش های میدانی، این مورد اغلب اتفاق نمی افتد. به عنوان مثال قانون هم پوشانی رعایت نمی شود، پرایمر زنی هنگام نصب نوار چسب سرد فراموش می شود یا دوباره یک پرایمر زیر مواد 2 لایه نوار انقباض حرارتی اعمال می شود. با همه این ها می توان وجود مشکل در عملکرد احتمالی را پیش بینی کرد. گواهی نصب DVGW GW 15 تنها یکی از اقدامات اضافی برای نصب درست در پروژه است.
آماده سازی لوله به عنوان نمونه ای از پوشش سرجوش
آماده سازی ناحیه پوشش
در کاربرگ DVGW GW 15، آماده سازی لوله به صورت زیر خلاصه شده است:
· سطح کامل باید تمیز (بدون گرد و غبار یا ذرات دیگر)، خشک (پیش گرم شدن در بالای نقطه شبنم) و عاری از مواد دیگر مانند روغن، گریس و غیره باشد. پوشش کارخانه باید تا زاویه 30 درجه شیب دار شود.
· سطح اتصال به طور کلی 400 میلی متر است. آماده سازی لوله همان طور که در زیر توضیح داده شده است در آلمان برای همه مواد پوششی کاربردی مانند نوارهای سرد، نوارهای قیر، نفت خام و محصولات انقباضی استاندارد شده است. برای سیستمهای GRP، EP و PUR، دستورالعملهای نصب سازنده باید رعایت شود.
آماده سازی سطح فولادی
سطح فولادی باید عاری از گرد و غبار و سایر مواد خارجی باشد. پوشش موقت انتهای لوله باید برداشته شود. برای برداشتن پوشش 3LPE لوله ، پذیرفته شده است که سطح فولادی طبق الزامات SA 21/2 و DIN 55928 بخش 4 آماده می شود. در این موارد کافی است آن را با برس فولادی یا کاغذ سنباده تمیز کنید تا لایه برداری مورد نیاز به دست آید. برای [پلی اورتان] EP، PUR[اپوکسی] و GFK[پلاستیک تقویت شده با الیاف شیشه] لازم است ناحیه پوشش بلاست شود (SA 21/2).
در مورد پوششهای خمشی یا سایر قطعات بدون پوشش کارخانه، مهم است که متوجه باقی ماندن پلیسه روی سطح شوند. اگر چنین است، باید سندبلاست شوند.
لولههای با پوششهای پلیاتیلن 3 لایه و پوششهای PP[پلی پروپیلن]، چسبها و EP را میتوان در دسته پوشش میدانی گنجاند. چسب و EP باقی مانده از پوشش کارخانه باید سابیده شده و با یک پاک کننده پلی اتیلن تمیز شود.
آماده سازی PE
به عنوان یک قاعده کلی، انتهای پوشش های کارخانه ای زاویه دار هستند. با توجه به نوع پوشش میدان مورد استفاده، باید اطمینان حاصل شود که نصب می تواند بدون فضای خالی انجام شود. اگر این را نمی توان تضمین کرد، به عنوان مثال اگر انتهای پوشش ها صاف باشد یا اگر پوشش کارخانه ای آسیب دیده باشد، انتهای آن باید به صورت دستی با یک اسکریپر آماده شود.
آماده سازی سطح پوشش داده توسط پلی اتیلن برای کیفیت پیوند پوشش میدانی مهم است. اکسید باقی مانده بر روی سطح PE/PP باید با تمیز کردن و سایش (برس فولادی یا کاغذ سمباده) جدا شود. این آماده سازی حداقل 100 میلی متر بر روی پوشش اعمال شده کارخانه همپوشانی دارد.
برای پوشش های کارخانه ای EP، PUR و GRP[فایبر گلاس] باید دستورالعمل های نصب سازندگان رعایت شود.
پرایمر
به جز نوارهای پترولاتوم و برخی محصولات 2 لایه انقباض حرارتی، پرایمر برای همه نوارهای محافظ در برابر خوردگی مورد نیاز است. فقط استفاده از پرایمر سازگار با سیستم مجاز است. قبل از اعمال پوشش، پرایمر باید خشک شود. استفاده از مشعل برای تسریع فرآیند خشک کردن مجاز نیست. اگر پرایمر بیش از 24 ساعت در معرض شرایط آب و هوایی قرار گیرد باید دوباره روی سطح لوله اعمال شود.
باید توجه ویژه ای به این واقعیت داشت که بیشترین خطاها به همین دلیل رخ می دهد. پرایمر لوله فقط تا حدی خشک شده یا اصلاً خشک نشده است. خاک یا ذرات دیگر روی سطح باقی می ماند یا سابیده نشده است. در این مورد، دیگر نمی توان از محافظت در برابر خوردگی کافی از سیستم صحبت کرد.
همان طور که قبلا توضیح داده شد، سطوح باید قبل از اعمال یک پوشش میدانی در یک حالت مشخص قرار گیرند. استفاده از این شرط به این معنی است که در شرایط میدانی انجام این کار بسیار دشوار است. علاوه بر این، عملکرد فردی نصب کننده نیز یک متغیر مهم در کیفیت پوشش های میدانی است (مخصوصاً برای روکش ها) و فشار مازادی که فضای بسیار کمی را برای نصب های پر زحمت باقی می گذارد، نباید نادیده گرفته شود.
با در نظر گرفتن این موضوع، بدیهی است که این سؤال در مورد تأثیرات کاربردهای ضعیف مطرح شود: مثلاً برای سطوحی که سندبلاست نشده اند چه اتفاقی می افتد؟
به همین دلیل یک چسب حساس به فشار در جهت بهبود مستمر محصول ایجاد شد؛ برای کشف این که چگونه آماده سازی سطح غیر استاندارد بر چسبندگی تاثیر می گذارد؟ محصول تحت شرایط واقعی میدانی چگونه رفتار می کند؟ آزمایش لایه برداری و برش انجام شد. قطعات لوله آزمایش با قطر اسمی 100 میلی متر برای آزمایش به روش DIN 30 672 تهیه شد (جدول 1).
شماره | آماده سازی سطح | دمای پیش گرم کن | توجه |
1-3 | SA2 1/2 | 60 | مطابق DIN 30672 |
4-6 | SA2 1/2 | هیچ | - |
7-9 | کاغذ سمباده K40 | 60 | - |
10-12 | کاغذ سمباده K40 | هیچ | - |
13-15 | برس فولادی | 60 | - |
16-18 | برس فولادی | هیچ | - |
19-21 | هیچ | 60 | - |
22-24 | هیچ | هیچ | تست لایه برداری روی فولاد با سطح کمی خورده شده. بدون ذرات آزاد روی سطح |
توصیه (مبنای تمام آزمایشات DIN ) این است
· پیش گرم کردن تا 60 درجه سانتی گراد
· سایش سطح طبق SA 21/2
بنابراین شرایط بهینه برای پوشش های میدانی ایجاد می شود.
این شرایط به ندرت در وضعیت آماده سازی لوله به دست می آید. در سری آزمایشی 4 تا 24 بدتر می شود تا جایی که:
· بدون پیش گرم کردن
· بدون حذف زنگ زدگی یا آماده سازی دستی دیگر (سابیدگی)
وضعیتی که هرگز نباید در عمل دیده شود.
برای حفظ فشار DIN مورد نیاز در آزمایش از دستگاه خاصی استفاده شد که نیرویی برابر با 5 نیوتن (با فنرها) به ناحیه چسبندگی ایجاد کرد. شکل 2 و 3 ساختار این دستگاه را نشان می دهد .
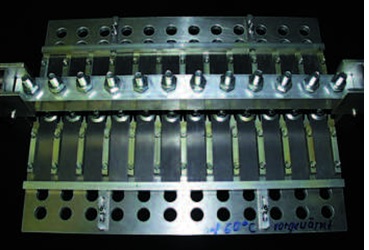
شکل 2: نمای کلی
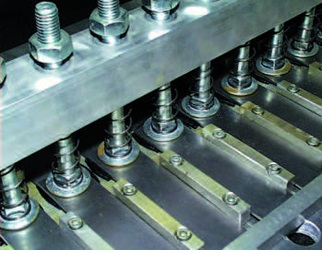
شکل 3: اعمال نیروی ثابت توسط فنر
شکل 4 نمونه های آزمایشی را پس از آزمایش لایه برداری نشان می دهد.
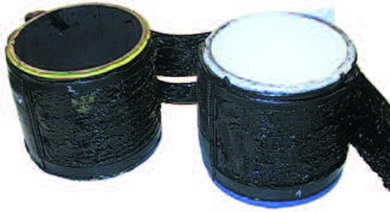
شکل 4: بدنه نمونه DN 100 بعد از آزمایش لایه برداری
به منظور تمایز، آزمایشهای اضافی روی لولههای با پوشش پلیاتیلن انجام شد. نتایج آزمون های زیر در شکل 5 مشاهده شد.
· آزمون لایه برداری بر روی فلز و پلی اتیلن
· آزمون برشی بر روی ورق های فلزی
نتایج حاصل از لایه برداری و استحکام برشی با یکدیگر مطابقت دارند، بنابراین شواهد عملی از کیفیت کاربرد در شرایط نامطلوب ارائه می شود. این دو کمیت به هم مرتبط، ضروری بودند تا بتوان اظهار نظری قطعی و مرتبط داد.
همه نتایج بالاتر از مقادیر مورد نیاز DIN 30672 هستند. نه تنها استحکام کششی از حداقل انتظار 5N/cm2 فراتر می رود، بلکه نتایج لایه برداری نیز با هر مقدار اندازه گیری شده از 15N/cm2 نیز فراتر می رود.
در کمال تعجب، آماده سازی سطح نمونه آزمایشی هیچ تاثیر قابل اندازه گیری بر نتایج نهایی نداشت.
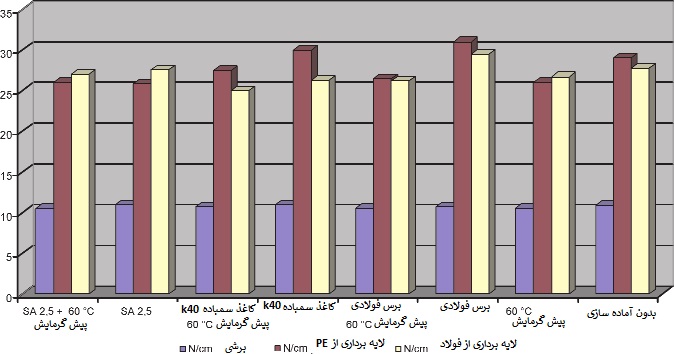
شکل 5: نتایج سری تست لایه برداری و برشی
خلاصه - نتیجه گیری برای تمرین آینده
این آزمون که از معیار پذیرش فراتر رفت، نتایج رضایت بخشی به دست آورد که به تحقیق و توسعه بیشتر چسب ها در عمل بسیار مرتبط است. حتی در شرایط نامطلوب (به ویژه برای پیوندهای چسبنده) پیوندی حاصل شد که از نظر حفاظت در برابر خوردگی، بالاتر از مقادیر استاندارد مورد نیاز بود.
اهداف تعیین شده برای چسب به دست آمده:
· ویسکو الاستیسیته
· چسبندگی در دمای پایین
این ویژگی ها باید در ارتباط با لایه پشت بند انقباض پذیر حرارتی ارزیابی شوند، زیرا چسب به تنهایی محافظت در برابر خوردگی کافی را ایجاد نمی کند. فرمولاسیون چسب ماده ای نرم و چسبنده تولید می کند که به دلیل خواص فیزیکی آن قادر به دستیابی به الزامات استحکام مکانیکی نیست. با رئولوژی (علم جریان و تغییر ماده) مناسب و نسبت پلیمر اصلاح شده لایه پشت بند به رزین اپوکسی و کنار گذاشتن چسبندگی منسجم که در هر صورت برای حفاظت در برابر خوردگی نیازی نیست، امکان بهینه سازی چسب فراهم شد. چسب حساس به فشار در زیر مواد پشت بند اعمال شده و تحت فشار دائمی توسط نیروی انقباضی در شرایط ایده آل قرار می گیرد.
مواد لایه پشتی در وهله اول یک برنامه حفاظتی در برابر خوردگی ایجاد می کند. و باید بتواند فشار فرورفتگی شدید را تحمل کند. این کار توسط پلی اتیلن با چگالی بالا با ضخامت لایه کافی (بیشتر از 1 میلی متر) تضمین می شود.
مواد پشتی پلی اتیلن با چگالی بالا مورد استفاده در این سیستم حفاظت در برابر خوردگی به نیروی انقباضی نشان داده شده در شکل 6 دست یافت.
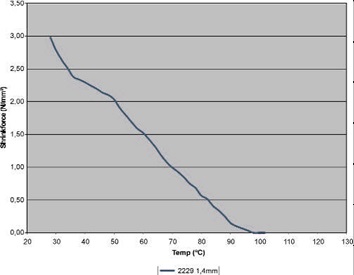
شکل 6: نمودار نیروی انقباضی وابسته به دما برای طیف وسیعی از مواد پایه HDPE
پس از خنک شدن نواحی کریستالی مواد پشتی متقاطع، نیروی انقباض مواد پشتی با پیوند پیچیده از محدوده افزایش می یابد, 2.5N/mm2 تا تقریبا 3N/mm2 در 30 درجه سانتی گراد ( تقریباً 135 کیلوگرم برای عرض روکش استاندارد 450 میلی متر). از این ترکیب چسب "نرم" و نیروی انقباض بالا یک "اثر خود ترمیمی" مثبت و ایمن حاصل می شود (شکل 7).
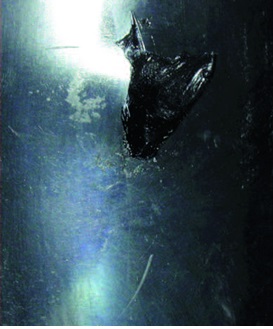
شکل 7: اثر خود ترمیمی در صورت آسیب به مواد پایه HDPE
تحت فشار بودن مواد پشتی و به دلیل چسبناک بودن رفتار چسب، عیب خود را در خود ترمیم می کند.
از شرایط استفاده همان طور که در بالا به طور مکرر ذکر شد و باید نکات زیر را در محل پروژه در نظر گرفت:
· آماده سازی مطابق با شرایط میدانی
· سرعت بالا (تاکید بر زمان و هزینه)
· آماده سازی اولیه و غیر حساس
این معیارها به سختی می توانند به صورت هنجار در نظر گرفته شوند، که به دلایل فنی باید به نتایج آزمایش هایی مانند مقاومت لایه لایه شدن و مقاومت برشی تکیه کنند.
به طور کلی برای نصب ایمن و آسان سیستم های حفاظت در برابر خوردگی در زمین باید نکات زیر را در نظر گرفت:
· هرچه قطعات منفرد کمتری در هر برنامه استفاده شود، نصب در این زمینه آسان تر خواهد بود.
· هر چه کارهای دستی کمتری انجام شود، اشتباهات کمتری انجام خواهد شد.
· هرچه از سیستمهای متفاوت کمتری استفاده شود، نصاب کمتر گیج میشود (بدون سردرگمی در مورد اینکه کدام جزء باید برای کدام سیستم استفاده شود)
· هرچه سیستم نصب کردن مسائد تر باشد ، محافظت در برابر خوردگی بهتر است.
سیستم محافظت در برابر خوردگی آزمایش شده از ترکیب مواد پشت بند پلی اتیلن با چگالی بالا با چسب، فوقالعاده مورد پسند جهت نصب است که آن را قادر میسازد تا محافظت در برابر خوردگی را تحت نامطلوبترین شرایط ارائه دهد. نصب آن سریع و آسان است و در یک مسیر قابل اعمال است.
این سیستم محافظت در برابر خوردگی نه تنها تمام الزامات فنی فعلی را برآورده می کند، بلکه جریان کار در محل را نیز بهبود می بخشد.
با این حال، حتی بهینه ترین سیستم پوشش دهی نمی تواند نقش آماده سازی اولیه لوله را قبل از نصب ایفا کند. ذرات باقیمانده گرد و غبار، زنگ زدگی یا لایه مرطوب منجر به خرابی عملکرد سیستم پوشش میدانی می شود.